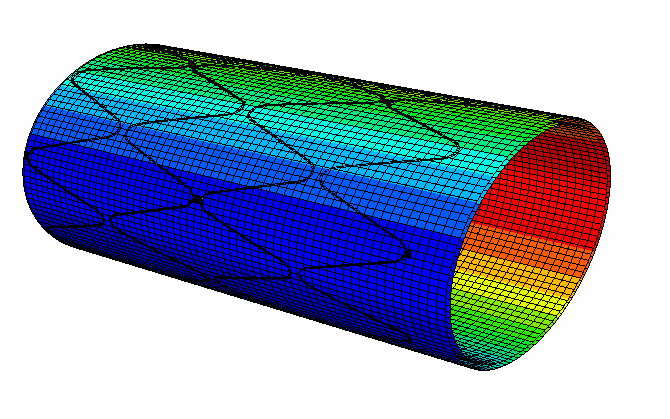
Impact Damage Analysis of Composite Plate
Impact Damage Analysis of Composite Plates; Low-velocity and high-velocity impact simulation on composite structures is a phenomenon that engineers in various industries such as aerospace, marine, and automotive should focus more on. In this FE project, the impact on the composite laminate was studied by Abaqus and LS-Dyna finite element software.
In order to perform an impact damage analysis of composite plate, the model of the composite material was used along with the degradation criterion and damage evolution This model has the ability to grow damage gradually. Many problems related to numerical simulations such as instability and dependence of the results on the element size tried in this model are reduced as much as possible.
impact damage analysis of composite plates using finite element modeling allows studying how impact events cause damage initiation, progression and final failure. The results provide insights into optimizing laminate designs, materials and processing to improve impact resistance of composite structures.
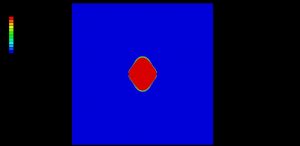
Impact Damage Analysis of Composite Plate
Composite Impact Resistance
Comparing several different plates, it was concluded that the composite impact resistance is good. In low-velocity impact damage analysis of composite plate in order to better analyze different modes of damage can be seen. These modes include matrix cracking, fiber breakage, and kinking, etc. To simulate delamination, the Cohesive Zone Model was used because of its advantages over other methods, such as the VCCT method in Abaqus.
A combination of modifications to a composite laminate‘s stacking sequence, thickness, materials, internal geometry and microstructure can lead to significant improvements in impact damage resistance. Selecting the right combination depends on the impact conditions and failure modes that need to be mitigated for a specific application.
Impact Damage Analysis of Composite Plate Achievements
- Writing Fortran user subroutines (VUMAT & USDFLD) to predict composite plate failure by Hashin, Puck, and maximum stress failure criteria in Abaqus
- Delamination simulation and prediction by various Tie_break, Cohesive contact, etc.
- Determining the best material models for predicting the behavior of composites in LS-Dyna
- Familiarity with advanced methods of composite material modeling
- Familiarity with different methods of modeling laminates, Randomly chopped fiber, Filament winding, Woven in Abaqus and LS-Dyna
- Familiarity with plastic injection methods for needle composites
- Familiarity with different methods of predicting damage and failure and the differences and advantages of each in Abaqus and LS-Dyna software
- Verification & validation (V&V)
- Familiarity with and application of the latest model for predicting failure in composite materials called LaRC05, produced by NASA’s Langley Lab and used in Abacus
- Advanced and optimal coding of composite materials with high accuracy and computational speed
- Simulation and prediction of a low-cycle and high-cycle fatigue of some special composites with the help of writing subroutine and the use of specialized plug-ins
The goals of performing impact damage analysis of composite plates are to:
• Predict the impact energy that will cause the failure of the composite plate
• Determine the sensitivity of the laminate to different impact conditions
• Identify the critical failure modes (delamination, fiber breakage, etc.)
• Study the effects of laminate parameters like ply orientations, stacking sequence and layer thickness
• Evaluate the performance of different composite materials under impact loads
• Optimize the laminate design for maximum impact damage resistance
The benefits include:
• Virtual prototyping – Testing “virtual” plates to determine failure limits instead of conducting many physical impact tests
• Design optimization – Modifying laminate parameters to reduce impact damage and improve resistance
• Cost reduction – Less need for physical testing of updated designs
• Failure prediction – Determining the impact energy and conditions that will cause the failure of a given laminate design
• Insights into failure mechanisms – Better understanding of how impact loads cause different failure modes within composite laminates
For more information contact us.