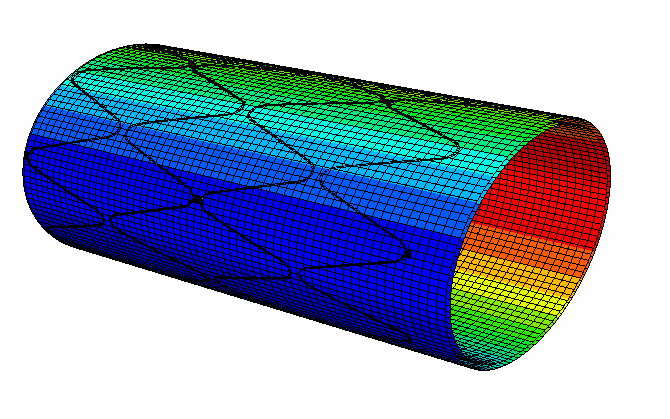
Low-Velocity Impact Induced Damage in Composite Overwrapped Pressure Vessel
Abaqus finite element software allows modeling low-velocity impact induced damage in composite overwrapped pressure vessel using a 2D or 3D Hashin VUMAT (user material subroutine). Low-velocity impact can cause significant internal damage in composite overwrapped pressure vessels (COPVs) that is not visible externally. Modeling such impact damage in COPVs using finite element analysis can provide useful insights. A Hashin 3D VUMAT can be implemented to predict various damage modes in the FRP composite – fiber tension/compression failure, and matrix tension/compression failure. Modeling low-velocity impact damage in COPVs using Abaqus with a composite damage model like 3D Hashin VUMAT can provide valuable insights into failure mechanisms, residual strength and impact resistance. Such models can be validated using experiments and used to evaluate design improvements for better impact performance.
Various low-velocity impact induced damages can occur on the composite structures during manufacturing, operation, and maintenance processes.
Therefore, the impact damage and residual strength of the composite structures have been important issues in the FRP composite industries. The impact damage needs to be considered in the design step and an efficient analysis tool is required to analyze the impact damage and residual strength of the composite structures.
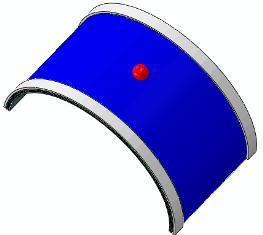
Low-Velocity Impact Induced Damage in Composite Overwrapped Pressure Vessel with Abaqus & 3D Hashin VUMAT
Proposed Composite Damage Model
In this project, a phenomenological composite damage model based on continuum damage mechanics (CDM) was used for the impact and residual strength analysis of composite structures. A damage variable considering the energy release rate of composite strength was derived to simulate the progressive failure of the composite damage and it was employed in the proposed composite damage model. The irreversible strain due to damage was also considered in the damage model. Also, the nonlocal smeared cracking approach was considered to prevent the strain localization & mesh sensitivity problem which is popular in damage analysis. Among all existing failure criteria for FRP composite materials, after extensive studies, the 3D Hashin failure criterion was selected as the appropriate failure criterion for the proposed composite damage model.
A cohesive zone model was used to simulate the inter-laminar damage of composites. The damage model was implemented in the VUMAT user material subroutine of Abaqus/explicit. The effect of the damages on the residual burst pressure of the cylindrical composite pressure vessel was also investigated.
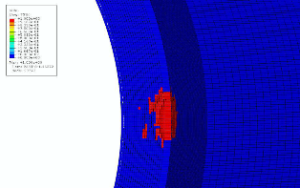
Low-Velocity Impact Induced Damage in Composite Overwrapped Pressure Vessel with Abaqus & 3D Hashin VUMAT User Material Subroutine
The analysis results such as the impact response, impact damage, and residual strength, were compared with the test data to verify the damage model and analysis methods.
VUMAT User Material Subroutine
A VUMAT user material subroutine allows you to define a custom material model in finite element analysis software. It gives you more flexibility beyond the built-in material models.
The VUMAT subroutine allows you to:
- Define your own constitutive model – This could be a plasticity model (like GTN damage model for metals), damage model, composite damage model, etc. You define the behavior of the material.
- Calculate stress and stiffness – The VUMAT must calculate the Cauchy stress tensor and material stiffness tensor based on the input strain and state variables.
- Update state variables – You can define state variables that evolve as the analysis progresses. The VUMAT updates these state variables at each increment.
- Predict damage initiation and evolution – For a damage model, the VUMAT can determine when damage initiates based on failure criteria (for example look at the 3D Hashin VUMAT code developed by BanuMusa R&D). It then evolves the damage as the analysis progresses.
- Consider nonlinearity – The VUMAT can model nonlinear material response due to plasticity, damage, large deformations, etc.
- Return data to Abaqus – The VUMAT returns the calculated stresses, stiffnesses, and updated state variables to Abaqus at each increment.
- Be more efficient – A VUMAT coded in a language like Fortran can be more computationally efficient than using built-in models.
The VUMAT defines the constitutive equations and material logic, while Abaqus takes care of the geometry, mesh, loads and analysis procedure. This allows sophisticated material models to be used within Abaqus.
In summary, a VUMAT user material subroutine gives you full control over how a material behaves in an analysis. It allows you to implement complex constitutive models and predict damage evolution, which is important for composite pressure vessels.