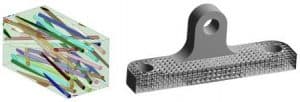
Micromechanics of Materials
Micromechanics of Materials
Micromechanics of materials is the study of how the microstructure and properties of materials influence their macroscopic mechanical behavior. It focuses on understanding and modeling the relationship between a material’s microstructure (e.g. grain size, defects, inclusions) and its mechanical properties (strength, stiffness, toughness, fatigue resistance, etc.) at the microscopic level.
It is not easy for finite element analysis / CAE engineers to simulate microstructures of materials (such as composite materials). If it is necessary to simulate the microstructure of the material, the volume of computations in finite element analysis simulation is so large that it is not possible to do it with any computer. If the geometry of the structure is also complex, the computational cost will increase. If the microstructure of the material is complex, the only way left to simulate it is to use the homogenization of the properties of the material. However, the use of micromechanical methods has found its place in computational mechanics in recent years, and more and more researchers are paying attention to it.
Homogenization Methods
Homogenization methods are techniques used to compute the effective properties of heterogeneous materials from the properties of their constituents. They involve “homogenizing” the properties of the complex microstructure into equivalent properties of a homogeneous material.
Common homogenization methods include:
- Analytical methods – These include Voigt, Reuss, and self-consistent schemes which make simplifying assumptions to analytically calculate the effective properties. They are simple but often inaccurate.
- Finite element homogenization – This involves creating a representative volume element (RVE) of the microstructure and applying periodic boundary conditions. An FE analysis is run and the homogenized response is used to determine effective properties. This is more accurate but computationally expensive.
- Computational homogenization – This performs full microscale simulations of response and failure. Effective properties are then fitted to the homogenized stress-strain curve. It captures microstructural effects but is very costly.
- Multi-level modeling – A coarse FE model is first analyzed. Then high-fidelity microscale models are created in regions of interest and coupled to the coarse model. Effective properties are updated iteratively.
The goal of homogenization is to:
- Replace the complex heterogeneous microstructure with an equivalent homogeneous material
- Define the mechanical properties of the equivalent homogeneous material
- Enable analysis and simulation at larger macroscopic scales
The computed effective properties include:
- Elastic moduli (e.g. Young’s modulus, shear modulus)
- Strength properties (yield stress, ultimate stress)
- Density
- Thermal and electrical conductivity
The choice of homogenization method depends on factors like required accuracy, available information, and computational resources. More complex approaches are generally more accurate but also more costly.
So in summary, homogenization methods provide a means of modeling heterogeneous materials as homogeneous solids with effective mechanical properties that adequately represent the microscale behavior.
Micromechanics in Abaqus
Micromechanics in Abaqus can be performed by the Micromechanics Plugin for Abaqus is a third-party plugin that facilitates multiscale modeling using the finite element representative volume element (FE-RVE) approach in Abaqus.
Some of the main functionalities it provides are:
- Parameterized generation of FE-RVE geometries for common microstructures like unidirectional composites and ellipsoidal inclusions. This simplifies creating the microstructure models.
- Application of different types of boundary conditions on the FE-RVE like periodic, Taylor, and Neumann boundary conditions. This allows simulation of the constraints and loads at the macroscale.
- The ability to drive the FE-RVE with load and field histories from larger-scale component analyses. This enables a true multiscale workflow.
- Simulation of various RVE physics like mechanical, thermal, and coupled analyses. The plugin supports both solid continuum and shell microstructures.
- Homogenization of the microscale response to determining effective material properties like elastic stiffness, thermal expansion, section stiffness, thermal conductivity, density, etc.
- Tools for post-processing the results like phase-averaged fields, histograms, and property extraction.
In summary, the plugin simplifies and automates many of the tedious tasks involved in setting up and analyzing FE-RVE models in Abaqus. This allows users to focus on the physics of the multiscale problem instead of the details of the FE model implementation.
Some of the main benefits it provides are:
- Time savings by automating repetitive tasks
- The reduced effort required to create parameterized FE-RVE geometries
- Simplified application of different boundary conditions
- Ability to integrate larger-scale and microscale analyses into a seamless workflow
- Accelerated determination of effective material properties from microscale simulations
So in essence, the Micromechanics Plugin for Abaqus streamlines the process of performing micromechanics analysis using the finite element representative volume element approach.
Micromechanics of Materials in Ansys
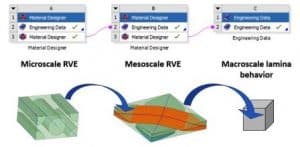
Micromechanics with Ansys Material Designer
In ANSYS Mechanical, there is a feature called ANSYS Material Designer that allows for optimizing the microstructure of the material and homogenizing its properties for advanced materials and FRP composites.
In the video below, the material designer demo in Ansys is explained for about 3 minutes.
Ansys Material Designer can calculate the temperature and elastic properties of a heterogeneous material such as that present in composite materials. To do this, the software defines a representative volume element (RVE) of the material microstructure. representative volume element is the smallest volume of matter that has the same characteristics as material at the macro scale. In Ansys Material Designer, FE engineers can define RVE with any shape and dimensions.
Using Ansys Material Designer, it is possible for engineers to analyze RVEs of any shape and size. Some of the predefined microstructures in Ansys Material Designer are listed below:
- Unidirectional Composites
- Woven composites
Ansys Material Designer RVEs
- Chopped Composites
In the software environment, it is possible to model other microstructures according to need.
After determining the homogeneous characteristics of the composite material in the material designer, the information obtained can be used in ANSYS Mechanical or ANSYS Workbench. By understanding the behavior of matter at the microscale and its effect on the macro behavior of matter, it is possible to optimize production according to need.
Micromechanical Failure Analysis with Autodesk Helius PFA
Autodesk Helius PFA is a software tool for performing multiscale failure analysis of materials. It can integrate microscale and macroscale simulations using a true two-way coupling. This enables more realistic failure predictions. Helius PFA supports a wide range of analysis types including static, dynamic, thermal, cyclical and fatigue. It can also perform optimization and probabilistic analysis. Helius PFA uses advanced failure criteria to predict failure initiation and propagation at the microscale and macroscale. It also helps identify failure hotspots within complex geometries. it can work with other tools like Moldflow and FEA solvers like Abaqus to enable an integrated workflow.
BanuMusa R&D Services
Modeling of various micromechanical models
- Definition of various boundary conditions in micromechanical models
- Definition of different micromechanical geometries in finite element analysis software
- Define and use different homogenization methods
- Predicting multiscale material failure | Autodesk Helius PFA | Abaqus Micromechanics Plugin | Ansys Material Designer | User subroutines
- Application of micromechanics in computational modeling of nanomaterials
- Application of micromechanics in medical modeling
- Study the effect of grain size on yield strength
- Compare the properties of monolithic and composite microstructures
- Determine the effect of voids and inclusions on ultimate tensile strength
- Simulate fatigue crack propagation at the microscale
Finite Element Analysis
- Abaqus (User subroutines, Python scripting, and plugins)
- Ansys
- Autodesk Helius PFA
BanuMusa R&D has conducted numerous FE research and projects to simulate the failure of composite materials using micromechanical methods.
Contact us for a free consultation and more information.