WCM Plugin
Wound composite modeler (Abaqus WCM Plugin) In the filament winding method, the resin-impregnated strands are twisted around a rotating mandrel to form a tubular shape or any possible axial symmetry structure. In the aerospace industry, the application of this production method is in the construction of rocket fuel vessels and rocket engine bodies. Its application in the automotive industry is mostly focused on fuel storage vessels for hydrogen cars. In recent years, in addition to these cases, this type of production method has been used in the manufacture of diving oxygen capsules and fire extinguishers due to the superior conditions of composites compared to metals.
Design and analysis of composite overwrapped pressure vessels
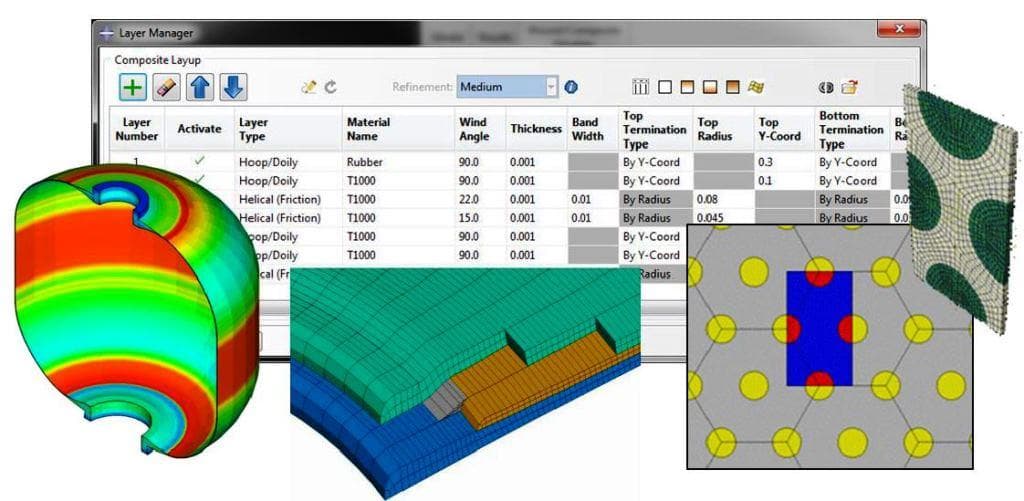
Plugin Name: Wound Composite Modeler for Abaqus
Version: 2016-1
Software: Abaqus
Application: Design and analysis of composite pressure vessels
In recent years, filament winding has become a widely used technique in the construction of various composite structures. The complexity of the analysis of this type of structure is the constant change in the direction of the fibers.
Abaqus Finite element software does not yet have the full ability to analyze such structures. For this reason, the WCM plugin for modeling and analyzing composite structures of helical strands, especially composite vessels, has been prepared by SIMULIA company to make the work of FEA engineers in Abaqus easier.
In this plugin, it is possible to model, change, and modify geometric details and various winding methods.
Method of production
In the filament winding method, the resin-impregnated strands are twisted around a rotating mandrel to form a tubular shape or any possible axial symmetry structure. In the aerospace industry, the application of this production method is in the construction of rocket fuel vessels and rocket engine bodies.
Its application in the automotive industry is mostly focused on fuel storage vessels for hydrogen cars. In recent years, in addition to these cases, this type of production method has been used in the manufacture of diving oxygen capsules and fire extinguishers due to the superior conditions of composites compared to metals.
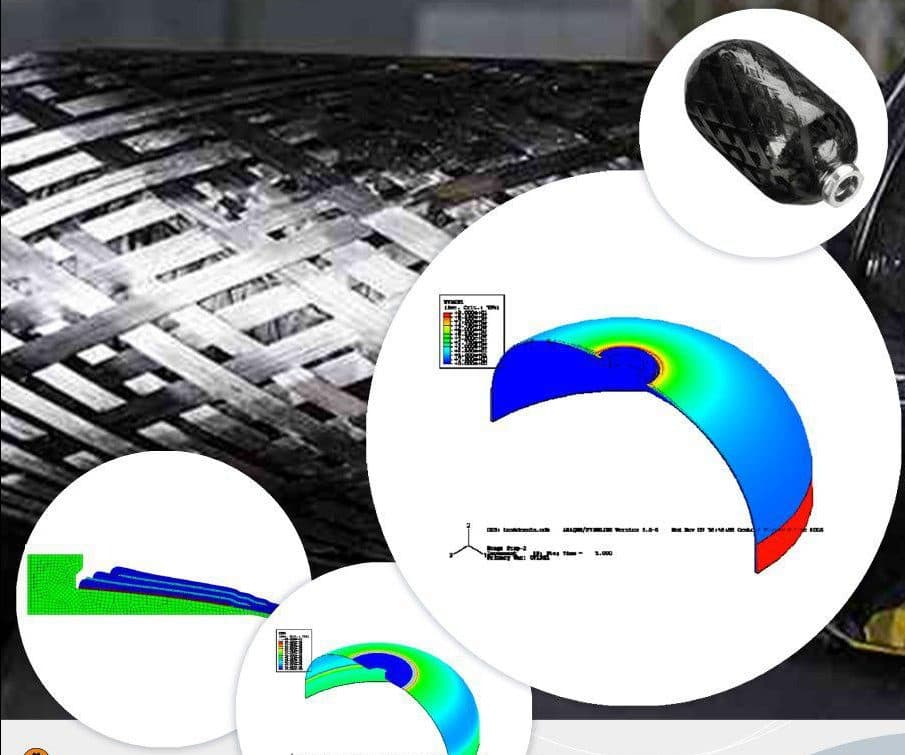
Manufacturing processes
The manufacturing of the composite pressure vessel with the filament winding method begins with the selection of the liner (including cylinders and domes). Both ends or one end of the umbilicus, which are usually metal, are inserted to connect the nozzle, valve, or any other part to the pressure vessel. Then a set of filaments is wound in a spiral around the liner to form layers. After the layers have reached a sufficient number, the vessel is placed in the oven to perform the cooking operation. Sometimes the liner comes out of the vessel. If there is a task for the liner while designing, it remains in the vessel. In some designs, a piece of rubber is used on the liner near the navel to control shear strains. Once the spiral layers of the domes are completely covered, the angle of rotation changes to cover the umbilical cord well.
Features of Wound Composite Modeler plugin
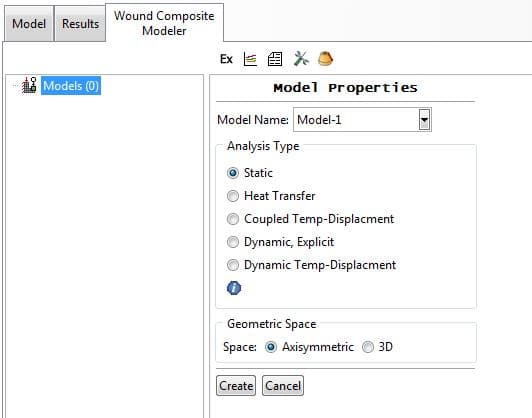
- Geometric modeling of domes in the form of elliptical, spherical, geodesic, or table of points of interest
- Apply specifications such as layer material, thickness, bandwidth, and winding angle
- Apply geodetic or non-geodetic winding pattern
- Locating and installing rubber shear layers and reinforcing fabrics
- Apply a variety of mesh generation methods
- Apply a variety of loads and boundary conditions
- Obtain and view results with different details
Watch a demo of the space of this plugin in the video below.