In this Abaqus tutorial, we will explore the Abaqus/CAE Plug-in Utility for calibrating Nitinol material behavior. We will walk through an example of calibrating the nitinol material model using experimental data. This will involve understanding the process of inputting experimental data, defining material properties, and using the utility to calibrate the material behavior based on the experimental results.
By the end of the tutorial, you will better understand how to use the Abaqus/CAE Plug-in Utility to calibrate Nitinol material behavior. Additionally, you can download the Abaqus file and the test data used in the example, allowing you to practice and apply the concepts discussed in this tutorial. This tutorial aims to provide a comprehensive guide for those looking to calibrate Nitinol material behavior in Abaqus, offering practical insights and hands-on experience with the process.
Nitinol Material Model: Understanding the Superelastic Behavior
Nitinol, a remarkable metal alloy, exhibits an extraordinary ability to undergo extensive deformations and still return to its original shape when unloaded. This unique characteristic has made it a fascinating material for various engineering applications, particularly in the field of biomedical devices and aerospace engineering.
While it is relatively simple to create a material model that accurately represents Nitinol’s behavior under uniaxial deformation, real-world applications often involve more complex loading scenarios. Historically, there has been a lack of widely accepted material models that can fully capture the intricate behavior of Nitinol. Hyperelasticity, commonly used to simulate rubber-like materials, has been a popular approximation for the loading phase of Nitinol’s behavior. However, recent advancements have led to the proposal of several other models, such as those by Auricchio and Qidwai, aiming to address the complexities of Nitinol’s behavior.
One of the key challenges in developing and verifying these models lies in the intricate manufacturing requirements of Nitinol. Typically available in the form of thin wires and tubes, the majority of testing data for Nitinol is derived from uniaxial experiments. While it is relatively straightforward to create a uniaxial model based on this data, accurately capturing Nitinol’s three-dimensional stress-strain behavior presents a much greater challenge.
At the heart of Nitinol’s complexity is its superelastic behavior, as depicted in Figure 1. In its austenite phase at rest, Nitinol undergoes a phase transformation to martensite when subjected to stress beyond a certain threshold. This transformation results in a significant amount of reversible strain, leading to the material’s superelasticity. The magnitude of the transformation strains, which can reach approximately 6%, sets Nitinol apart from conventional metals in terms of elastic behavior.
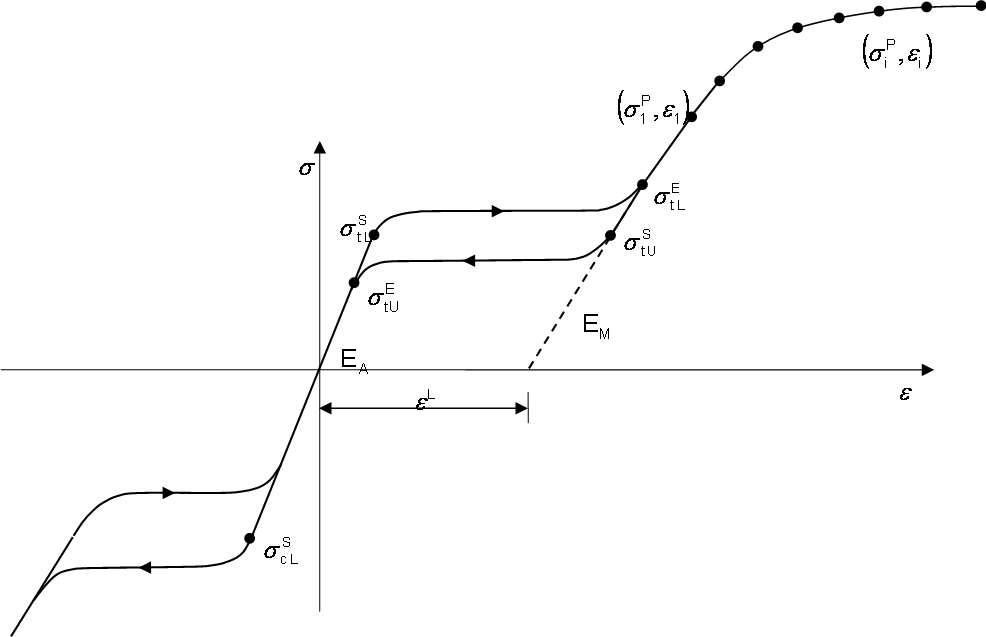
Figure 1: Uniaxial behavior of Nitinol
Upon further loading beyond the superelastic limit, Nitinol exhibits plastic behavior in the martensite phase. Calibrating an accurate material model for Nitinol in Abaqus requires comprehensive data on its uniaxial behavior, encompassing loading, unloading, reverse loading, and the influence of temperature effects (as shown in Figure 1).
Abaqus/CAE plug-in utility to calibrate Nitinol material behavior
Are you tired of manually inputting Nitinol material parameters into Abaqus/CAE? We have a solution for you! This plug-in provides a user-friendly interface to streamline the process of creating Nitinol material parameters based on uniaxial tension test data.
With just a few clicks, the plug-in generates necessary keywords and data lines automatically, saving you time and effort. It also follows the required naming convention for Nitinol materials, ensuring compatibility with Abaqus/CAE.
But that’s not all! The plug-in also offers an option to evaluate the material definition with a uniaxial 3D one-element model. This allows you to submit the analysis and view the results alongside the original test data for comparison. You can iterate this process by editing the points picked on the test data until the desired material behavior is achieved.
It should be noted that if you are using 3dexperience, you can do what this plugin does with the Material Calibration App.
If you are like me and you work with Abaqus, read the rest of the blog.
This plugin is used to determine the constants of nitinol material using laboratory test data. As you know, before Abaqus 2019, the superelasticity material model was available in Abaqus in the form of built-in routines of umat and vumat. In Abaqus 2019, the superelastic material model was added to the Abaqus CAE.
However, we still need to use this plugin to calibrate the material model. Everything is the same as before with only a few small changes that we will talk about in this blog.
Let’s start Abaqus tutorial
1- Plugin installation
After copying the plugin folder and extracting it in the Abaqus_plugins directory, open Abaqus/CAE. Go to the Property module. Open Calibration from the tree menu (Figure 2). Create a new calibration. When you double-click Behaviors, you’ll notice a small change. Yes, Nitinol Superelastic-plastic has been added (Figure 3). This was to make sure you added the plugin to Abaqus correctly. Click on Cancel to close the window.
Figure 2
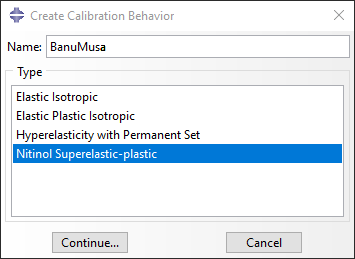
Figure 3
2- Enter the laboratory test data.
At this step, you can add test data to the table in two ways. 1- Import *.txt file of laboratory test data, or 2- Copy and paste it into the table (Figure 4).
Well, I am more comfortable with the second method. Here, enter as many tests as you have in separate data sets.
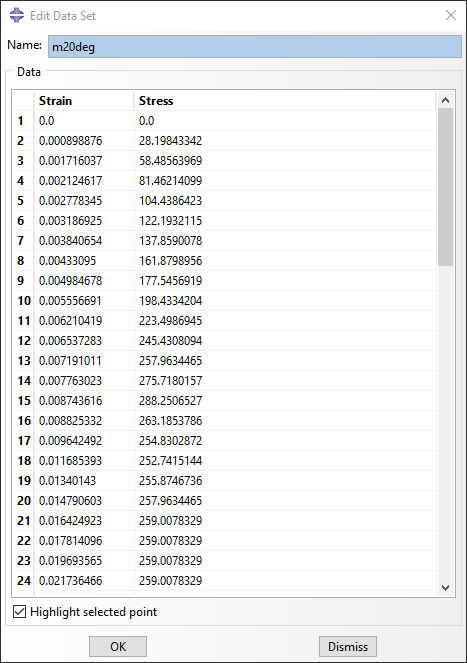
Figure 4
After importing the dataset, you can see the test chart.
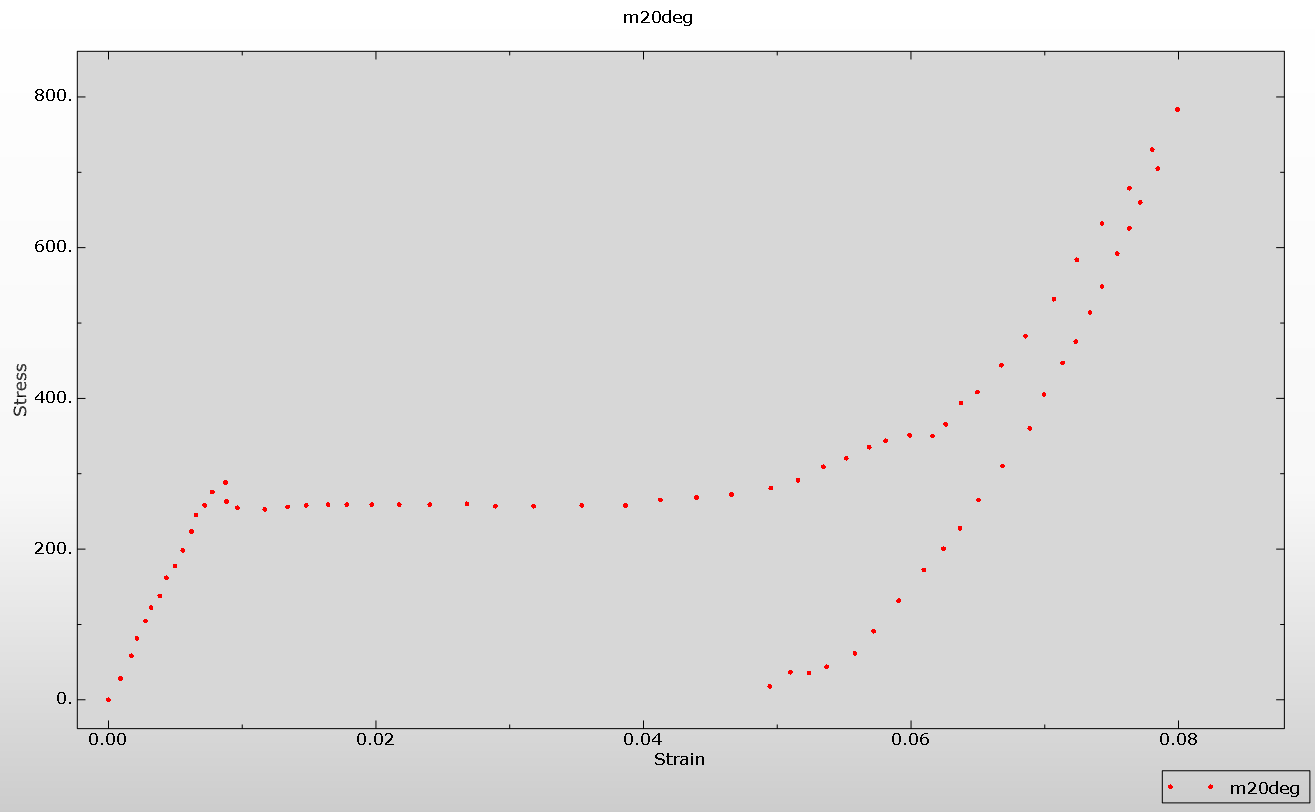
Figure 5
3- Build the calibration behavior.
In this step, you should double-click on Behaviors, choose Nitinol Superelastic-plastic, and then click continue, just like in the first step. The Edit Behavior window will open, similar to the one shown below. Next, select the dataset you want to calibrate and then pick points 1 to 5 in the Points tab.
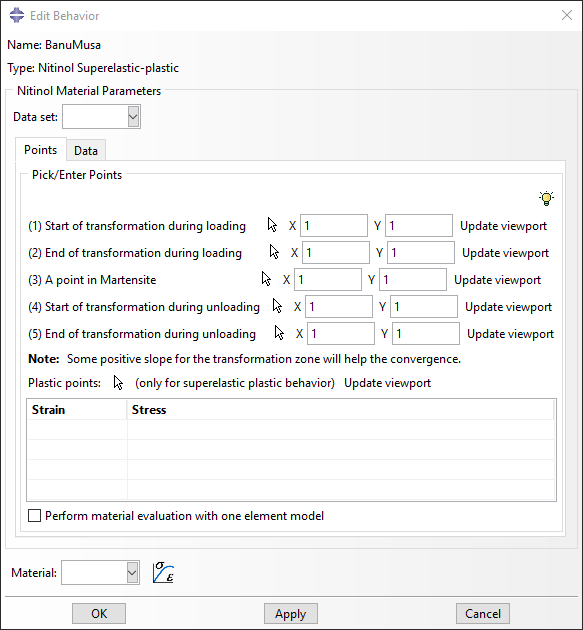
Figure 6
When a point is picked, the stress and strain values for that point will appear in the corresponding X and Y text fields. The stress-strain values for the selected points are used to calculate the Nitinol material constants. A tip button (located on the right side of the dialog) can help you identify the approximate locations of the points on the plot. It’s important to be careful when selecting the points, as having a positive slope between points 1 and 2, and between points 4 and 5, aids in the analysis convergence.
You can also modify the stress-strain point values from the plug-in dialog by directly editing the text fields. To see visual feedback on the changes made in the text fields, you need to click the Update viewport button. This will update the point locations and display the latest positions on the plot.
If you have plastic behavior (which is not applicable here), select several plastic points. The figure below provides an example.

Figure 7
Furthermore, the plug-in provides a feature to assess the material definition using a uniaxial 3D single-element model. If you choose this option, the plug-in will conduct the analysis and display the results alongside the original test data for comparison. You can repeat the process by adjusting the selected points on the test data until the desired material behavior is attained.
The tool for single-element evaluation generates a model with the assigned material, as well as the necessary load and boundary conditions, and then initiates a job for uniaxial tension analysis followed by post-processing. For each assigned material, a new single-element model is created in Abaqus/CAE and a job is submitted. During post-processing, the plug-in generates an X-Y plot of the analysis results for SDV22_EUTS (Equivalent uniaxial tensile stress) and SDV24_EUTE (Equivalent uniaxial tensile total strain), and displays it on the same viewport as the test data.
You can repeat the whole process by selecting the points again or by inputting different data in the plug-in dialog and running the single-element model until the desired material behavior is achieved.
Data Tab
Go to the Data tab. Choose standard or explicit analysis type here. I chose standard. Enter the number of times and annealing steps respectively. After that, it is necessary to enter mechanical constants such as Poisson’s ratio of austenite, martensite, and reference temperature. Next, enter the stress/temperature gradient in loading and unloading. The rest of the parameters should be entered based on the test data.
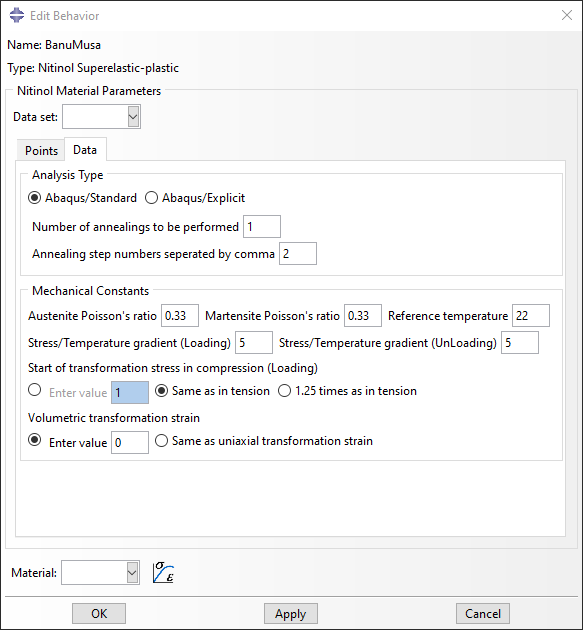
Figure 8
Click OK. The material name changes to ABQ_SUPER_ELASTIC_Material-1 for the standard solver or ABQ_SUPER_ELASTIC_N1D, ABQ_SUPER_ELASTIC_N2D, and ABQ_SUPER_ELASTIC_N3D for the explicit solver, depending on what solver you chose.
Open it. In this window, you can see Depvar and User Material. If you are using Abaqus older than 2019, there is no need to change anything.
![]() | ![]() |
If you are using Abaqus 2019 or later, you do not need to enter data in the Super Elasticity material model. You can analyze with the same information.
If for any reason you want to enter the data of the calibrated material model in the superelasticity material model, follow the table below.
Data | User Material[1] | Super Elsticity[2] | Material Model |
36321.99 | 1 | Young’s modulus of austenite | Elastic |
0.33 | 2 | Poisson’s ratio of austenite, | |
0 | 14 | Non-associated: volumetric transformation strain/ uniaxial transformation strain | Super Elasticity |
23682.92 | 3 | Young’s modulus of martensite | |
0.33 | 4 | Poisson’s ratio of martensite, | |
0.047 | 5 | Uniaxial transformation strain, | |
260.38 | 7 | Stress at which the transformation begins during loading in tension, | |
351.98 | 8 | Stress at which the transformation ends during loading in tension, | |
16.75 | 11 | Stress at which the reverse transformation begins during unloading in tension, | |
6.04 | 12 | Stress at which the reverse transformation ends during unloading in tension, | |
260.38 | 13 | Stress at which the transformation begins during loading in compression, as a positive value, | |
22 | 9 | Reference temperature, | |
5 | 6 | The slope of the stress versus temperature curve for loading, | |
5 | 10 | The slope of the stress versus temperature curve for unloading, |
[1] Abaqus 2018 or older
[2] Abaqus 2019 or later
Downloads
Plug-ins
Abaqus/CAE plug-in utility to calibrate Nitinol material behavior
INP files
Single-element evaluation with the built-in material model (2018 or older versions)
Single element evaluation with Super elasticity material model (2019 or later)
Test data
Nitinol test data (Auricchio 2014)
Conclusion
In general, there was no difference between the results of the Superelasticity model and the built-in utility of this model in Abaqus 2023 and 2017.
Using the plugin increases the speed of determining the parameters and constants of the nitinol material model.
References
– Pelton, Arthur R. “Hyperelastic Stress-Strain Behavior.” Rubber Chemistry and Technology 67.3 (1994): 481-493.
– Auricchio, Ferdinando, et al. “A finite element model for the design of NiTi stents.” Journal of the Mechanics and Physics of Solids 45.11-12 (1997): 1727-1750.
– Auricchio, Ferdinando, et al. “A model for nitinol hysteresis.” International Journal of Plasticity 12.5 (1996): 621-655.
– Qidwai, Muhammad A. “A thermomechanical constitutive model for shape memory alloys.” Journal of Intelligent Material Systems and Structures 11.10 (2000): 782-800.
– Abaqus Answer 1658