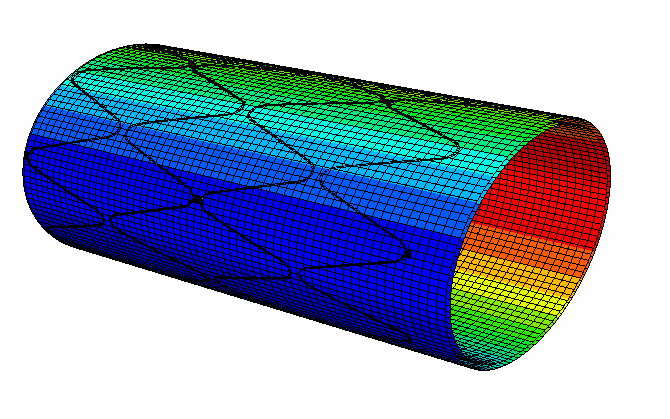
FRP Composite Dome with Traditional Persian Tiles
An FRP composite dome is a dome-shaped structure made of composite materials such as fiberglass and resin. These domes are typically used in a variety of applications, including architectural, industrial, and environmental. Here are some benefits and considerations of using FRP (Fiber-Reinforced Polymer) composite domes:
FRP Composite Dome Benefits:
- Lightweight:
FRP composite domes are lighter than traditional materials such as concrete or steel, making them easier to transport and install. - Corrosion-resistant:
The composite materials used in FRP domes are resistant to corrosion, making them ideal for use in harsh environments such as chemical plants or wastewater treatment facilities. - Design flexibility:
FRP composite domes can be molded into a variety of shapes and sizes, providing design flexibility for architects and engineers. - Durability:
FRP composite domes are durable and can withstand a wide range of temperatures and environmental conditions. - Low maintenance:
FRP composite domes require minimal maintenance compared to traditional materials, reducing overall lifecycle costs.
FRP Composite Dome Considerations:
- Cost:
FRP composite domes can be more expensive than traditional materials, although the cost can be offset by the benefits of reduced weight, maintenance, and durability. - Fire resistance:
FRP composite domes are not inherently fire-resistant and may require additional coatings or treatments to meet fire codes. - UV stability:
Exposure to UV radiation can cause degradation in the composite materials used in FRP domes, requiring the use of UV-resistant coatings or additives. - Manufacturing limitations:
The manufacturing process for FRP composite domes can be complex and may require specialized equipment and expertise.
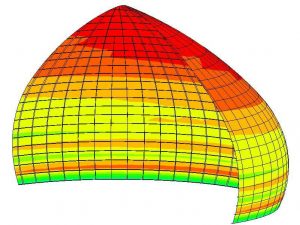
FRP composite dome
It takes about a year to build a dome by conventional methods, but the design of a FRP composite dome takes about 1 month and the execution of the dome takes about a week.
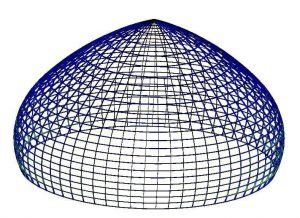
FRP composite domes
Our company with experience in engineering design and manufacturing this type of composite structure can participate in the design and construction of your FRP composite structures.
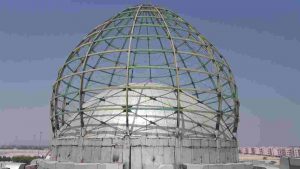
The old structure of the dome of the mosque
FRP Composite Dome Engineering Design
The engineering design of an FRP composite dome involves several steps:
- Determine the design requirements:
The first step in the engineering design process is to determine the design requirements for the FRP composite dome. This includes the size, shape, material properties, loading conditions, and environmental factors. - Select the material:
The next step is to select the appropriate composite material for the dome. This includes the type of fiber, resin, and additives, as well as any coatings or surface treatments. - Develop the geometry:
Once the material is selected, the geometry of the dome can be developed using computer-aided design (CAD) software. The dome’s structural elements, such as beams or trusses, can also be designed at this stage. - Analyze the dome:
The next step is to analyze the dome using finite element analysis (FEA) software. This involves applying the loading conditions and calculating the stress and strain in the dome’s structural elements. - Optimize the design:
If the analysis results do not meet the design requirements, the design can be optimized by adjusting the geometry, material properties, or structural elements and repeating the analysis. - Detail the design:
Once the design is optimized, the details of the dome’s construction can be developed. This includes specifying the manufacturing process, assembly sequence, and quality control procedures. - Manufacture the dome:
The final step is to manufacture the FRP composite dome. This involves fabricating the structural elements, applying the resin and fiber layers, and curing the composite materials.
Finite Element Analysis for Composite Structure Design
Here are some benefits of using finite element analysis (FEA) for composite structure design:
- It allows for more accurate stress analysis. FEA can simulate the actual loading and boundary conditions that a composite structure will experience in use. This gives a more precise stress distribution model than simplified calculations.
- It can optimize composite layer stacking sequences. FEA simulations can be run with different layer orientations and thicknesses to determine the stacking sequence that gives the best strength and stiffness for a given structure.
- It can predict failure modes. FEA can simulate failure mechanisms like delamination, fiber breakage, and matrix cracking. This helps identify potential failure points and weak areas in the design.
- It enables lightweight design. By simulating different design options, FEA helps optimize composite structures for maximum strength with minimum weight. This improves performance and efficiency.
- It reduces physical testing. Once an FEA model has been validated with physical test data, it can be relied on for design iterations and “what if” scenarios. This reduces the need for costly physical prototypes.
- It captures composite nonlinearities. FEA can accurately model the nonlinear material behavior of composites under different loading conditions, strains, and temperatures.
Manufacturing Process of an FRP Composite Dome
The manufacturing process for an FRP (Fiber-Reinforced Polymer) composite dome can be optimized in several ways to improve efficiency, reduce costs, and enhance quality. Here are some ways to optimize the manufacturing process of an FRP composite dome:
- Manufacturing techniques:
The manufacturing process can improve efficiency and reduce labor costs. techniques such as Hand lay-up, RTM, vacuum, pultrusion, or automated fiber placement can be used to produce consistent and high-quality composite material components. - Quality control:
Implementing a rigorous quality control program can help to identify and eliminate defects in the manufacturing process. This can include using non-destructive testing techniques, visual inspection, and statistical process control methods. - Mold design:
The design of the mold used to manufacture the composite dome can have a significant impact on the quality and efficiency of the process. A well-designed mold can reduce the amount of material waste, improve part consistency, and reduce cycle time. - Material selection:
Selecting the appropriate composite material and additives can improve the properties of the finished product and reduce manufacturing costs. This includes selecting the right type and amount of fiber, resin, and coatings. BanuMusa R&D, With the experience of its experts in designing composite structures, can calculate the best type of material, lay-up and manufacturing method with the help of FEA simulation. - Lean manufacturing:
Implementing lean manufacturing principles such as value stream mapping, continuous improvement, and waste reduction can help to optimize the manufacturing process. This can include reducing inventory, improving workflow, and minimizing downtime. - Process simulation:
Using simulation software to model the manufacturing process can help to optimize the process parameters and reduce the risk of defects. This can include simulating the resin infusion process, mold filling, and curing.