Built-in Material Models in Abaqus
ABAQUS has a number of little-known built-in material models that are not documented in the manuals and are hidden which you cannot access them. It is very easy but very practical.
These Abaqus material models are in the form of hidden Fortran user subroutines such as UMAT, VUMAT, UVARM, UDMGINI, etc., the code of which is available at the Abaqus installation directory, but is not accessible through the user interface. The reason for this may be a test by users or something like that.
Here I will introduce them to you and whichever you are interested in, you can order or shop.
1- Johnson-Holmquist (JH-1 & JH-2) & Johnson-Holmquist-Beissel (JHB) VUMAT for Ceramics and Brittle Materials
To predict the damage of brittle materials (e.g., ceramics) Johnson-Holmquist (JH-1 & JH-2) & Johnson-Holmquist-Beissel (JHB) material model in the form of a VUMAT subroutine for Abaqus/Explicit can be used. It can be used from the Abaqus 6.10 version. In this material model, it is possible to delete the element. The solution speed is almost good and depends on the number of elements.
These material models get 23 inputs and show 8 output variables to visualize the results. Shop now …
Hint: There is a similar model in LS-Dyna software called * MAT_JOHNSON_HOLMQUIST_CERAMICS in its material library.
2- Holmquist-Johnson-Cook (HJC) VUMAT Concrete Model
With the release of Abaqus 6.10, the constitutive model for concrete under impact loading conditions proposed by Holmquist, Johnson, and Cook (HJC) is available in the form of a built-in user material for Abaqus/Explicit. The Holmquist-Johnson-Cook (HJC) model is intended for the simulation of the mechanical response and failure behavior of concrete subjected to large strains, high strain rates, and high pressures.
The model is in the form of a VUMAT subroutine. This material model gets 23 material property inputs and shows 7 output variables to visualize the results. Order now…
3- LaRC05 Composite Failure Criteria (UVARM & UDMGINI)
The LaRC05 failure criteria is intended for laminated polymeric-matrix fiber-reinforced composites consisting of unidirectional plies and has been implemented in the form of two built-in user subroutines:
- The first one is a built-in UVARM user subroutine that evaluates the LaRC05 damage criterion and provides an output of damage tolerance. The option is available for both 2D and 3D stress states and is supported for plane stress elements (S4, S3, S4R, S3R), continuum shell (SC6, SC6R, SC8, SC8R), plane stress (CPS family), membrane (M3D family) elements and three-dimensional stress-displacement continuum elements (C3D4, C3D6, C3D8R, C3D10M).
- The second option is a built-in damage initiation (UDMGINI) user subroutine that can be used with XFEM-enriched elements to evaluate the onset of crack initiation and propagation. It is available only for 3D stress states and the family of three-dimensional stress-displacement continuum elements for which XFEM is supported.
It is just for Abaqus/Standard Solver and was introduced in 2017. LaRC05 failure criteria material model gets 15 material property inputs and shows 4 output variables to visualize the results. Shop now…
4- Multilinear Kinematic Hardening UMAT Model for Cyclic Plasticity
For Abaqus/Standard Solver 6.6 and higher versions, a multilinear kinematic hardening constitutive model (also known as the Overlay model) is provided in the form of a UMAT user subroutine. The Multilinear Kinematic Hardening Model for Cyclic Plasticity model is based on the original work of Besseling [1]. The material model is assumed to have various subvolumes, which have different yield strengths but the same elastic modulus and are subjected to the same total strain.
Multilinear kinematic hardening model for cyclic plasticity in Abaqus by UMAT built-in material model subroutine
The behavior of each subvolume is elastic-perfectly plastic. When multiple subvolumes are combined together, complex material behaviors, such as multilinear hardening and the Bauschinger effect, can be modeled. This model can be used to simulate fatigue and ratcheting of metallic materials. Order now …
5- UMAT Subroutine / VUMAT Subroutine for Elastic-plastic Simulation of Nitinol
For Releases 6.5-1 and higher of Abaqus, a constitutive model to simulate the superelastic behavior of alloys such as Nitinol (a nickel-titanium alloy commonly used in medical devices, such as cardiovascular stents and orthodontic wires) at finite strains is provided in the form of a built-in user material model for both Abaqus/Standard and Abaqus/Explicit. UMAT / VUMAT Subroutines for Elastic-plastic Simulation of the Nitinol model have been well-tested and performed robustly for all applicable elements.
Hint: Plasticity effects are included in Releases 6.10-1 and higher.
Alloys such as Nitinol exhibit superelastic behavior as they undergo reversible phase transformations between the austenite phase and martensite phase, both phases being linear elastic. This transformation produces a substantial amount of strain, which upon unloading is reversible.
The model is based on an additive strain decomposition, in which the total strain is taken as the sum of the elastic strain, the transformation strain, and the plastic strain. Plastic strains develop as soon as the material is loaded beyond full transformation. The transformation strain is of the order of 6%, but the elastic strain is much smaller and should be limited to a maximum of 2%. Since the transformation strains are large compared to typical elastic strains in a metal, the material is said to be superelastic [2].
The material data required by the model are obtained from straightforward observations of uniaxial tests. The data characterize the start and end of the phase transformation during loading, unloading, and reverse loading. The different elastic constants for the austenite and martensite phases are accounted for and user control of volumetric transformation strains is allowed. Temperature effects are included as well.
The elements that are supported for use with the material model are:
- 3D solids
- Plane strain
- Axisymmetric
- Plane stress
- 3D shells
- 3D membranes
- 3D beams
6- VUMAT User Subroutine Material Model for Molded Plastics
The following applies to Abaqus 6.8 and higher. Abaqus/Explicit contains a constitutive model for the simulation of molded plastics. It is implemented as a built-in VUMAT user subroutine. The model is intended to simulation of the mechanical response and failure behavior of molded thermoplastic materials under dynamic loadings, such as in crash and drop applications.
The VUMAT User Subroutine Material Model for Molded Plastics model is applicable to both fiber-reinforced and non-reinforced plastics and accounts for orientation-dependent plasticity and failure properties. The model is currently supported for plane strain, plane stress, and 3D elements that use full or reduced integration.
This includes the shell, continuum shell, membrane, 3D solid, 2D axisymmetric, and generalized plane strain elements. User materials are currently not supported in Abaqus/Explicit for small-strain shell elements (S4RS). Order now…
7- VFABRIC User Subroutine Material Model for Woven Fabrics
Woven fabrics are used in a number of engineering applications across various industries, including such products as automobile airbags, flexible structures like boat sails and parachutes, reinforcement in composites, architectural expressions in building roof structures, protective vests for military, police, and other security circles, and protective layers around the fuselage in planes. The Abaqus FABRIC model is a VFABRIC user subroutine-based material used to simulate woven fabrics in Abaqus Explicit.
So, if you want to model and predict the material damage of woven composites, you no longer need to write a user subroutine and you can use the same ready-made and attractive model. Order now …
8- VUMAT for Fabric Reinforced Composites
VUMAT user subroutine for fabric reinforced composites was introduced in Abaqus/Explicit 6.8. The model has been implemented as a built-in VUMAT user subroutine. The fabric reinforced composite model is currently supported for plane-stress elements; this includes Shell (S4R and S3R), continuum shell (SC6R and SC8R), plane stress (CPS family), and membrane (M3D family) elements. User materials are currently not supported in ABAQUS/Explicit for small-strain shell elements (S4RS).
The fabric-reinforced ply is modeled as a homogeneous orthotropic elastic material with the potential to sustain progressive stiffness degradation due to fiber/matrix cracking, and plastic deformation under shear loading.
The VUMAT subroutine model is capable of deleting elements. It has 16 output variable to show in the visualization module and get 7 elastic parameters, and 19 damage parameters material data inputs. Order now …
9- VUMAT subroutine for Bergstrom-Boyce Hysteresis Model for Viscoelastic Rubber-like Materials
Viscoelastic rubber-like materials often exhibit hysteresis in cyclic loadings. This behavior arises from the frictional sliding of the long molecules across one another. Bergstrom and Boyce [3] observed in experiments that both filled and unfilled elastomers show significant amounts of hysteresis during cyclic loading, and both filled and unfilled elastomers are strain-rate-dependent.
Based on the work of Bergstrom and Boyce [3], the model is meant for the simulation of large-strain, time-dependent hysteretic behavior in rubber-like elastomers. Order now…
There are 6 other material models besides these models that I will add to this in the future. As you can see the whole thing in Abaqus not only its graphical interface and hiding tools, plug-ins, Fortran subroutines and Python scripts are great that you can easily use them.
- J.F. Besseling, “A Theory of Elastic, Plastic, and Creep Deformations of an Initially Isotropic Material Showing Anisotropic Strain-Hardening, Creep Recovery, and Secondary Creep.” Journal of Applied Mechanics, pp. 529-536, 1958.
- ‘Simulation of implantable nitinol stents,’ Nuno Rebelo, Norm Walker and Hoss Foadian, Proceedings of the 2001 Abaqus Users conference
- Bergstrom, J. S., and Boyce, M. C., “Constitutive Modeling of the Large Strain Time Dependent Behavior of Elastomers,” Journal of the Mechanics and Physics of Solids, Vol. 46, No. 5, 1998, pp. 931–954.
3D Hashin USDFLD Subroutine Failure Criteria for Abaqus
VUMAT Subroutine: Shear Anisotropic Modified GTN Damage Model
Abaqus Tutorial: LaRC05 Failure Criterion For Fiber-Reinforced Composites
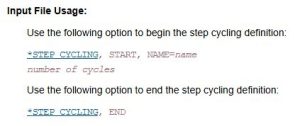
Understanding Step Cycling in Abaqus 2025
Understanding Step Cycling in Abaqus 2025 Introduction to Step Cycling Step cycling is an essential feature introduced in Abaqus 2025,
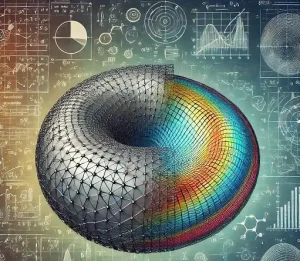
Uncertainty Quantification in Finite Element Analysis (FEA)
Uncertainty Quantification in Finite Element Analysis (FEA) In the domain of Linear Elasticity, certain problems have known theoretical solutions. For
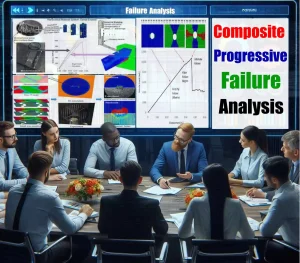
Composite Progressive Failure Analysis
Composite Progressive Failure Analysis As engineers working with advanced composite materials, one of the toughest challenges we face is accurately