Chang-Lessard Failure Criteria
Matrix compression failure criterion has the same form as that for matrix tensile cracking since the previous two failure mechanisms cannot occur simultaneously at the same point. After the failure index exceeds 1.0, both the transverse stiffness and Poisson’s ratio of the ply drop to zero.
It was evident that, unless the shear stress vanishes exactly, fiber-matrix shearing failure occurs before fiber buckling. However, fiber buckling may follow after fiber shearing because only the shear stiffness degrades after fiber-matrix shearing failure. Fiber buckling in a layer is a catastrophic mode of failure. Hence, after this failure index exceeds 1.0, it is assumed that the material at this point can no longer support any loads.
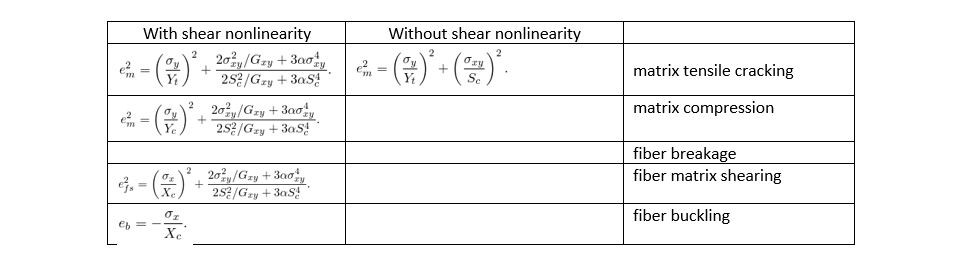
Chang and Lessard assume that after the failure occurs, the stresses in the failed directions drop to zero immediately, which corresponds to brittle failure with no energy absorption. This kind of failure model usually leads to immediate, unstable failure of the composite.
This assumption is not very realistic in reality, the stress-carrying capacity degrades gradually with increasing strain after the failure occurs. Hence, the behavior of the FRpcomposite after the onset of failure is not likely to be captured well by this damage model.
Moreover, the instantaneous loss of stress-carrying capacity also makes the post-failure analysis results strongly dependent on the refinement of the finite element mesh and the finite element type used.
Abaqus USDFLD subroutine example
Chang-Lessard failure criteria can be used with USDFLD & VUSDFLD user subroutines for damage analysis in standard and explicit Abaqus solvers from example 1.1.14 Abaqus Example Problem Guide is available.
3D Hashin USDFLD damage model with shear nonlinearity of Chang-Lessard model
I have studied different failure criteria models of composite materials. Here you can find FRP composite failure criteria in ABAQUS.
The advantage of the Chang-Lessard model is that it considers the nonlinear shear in the damage equations. The thing that has been seen in fewer damage models. Its importance is that at an angle of 45 degrees, the shear behavior of unidirectional laminated composites is very sensitive.
So, I tried to add this feature to the 3D Hashin damage Abaqus model and the results were interesting. You can see more information about the developed 3D Hashin model here.
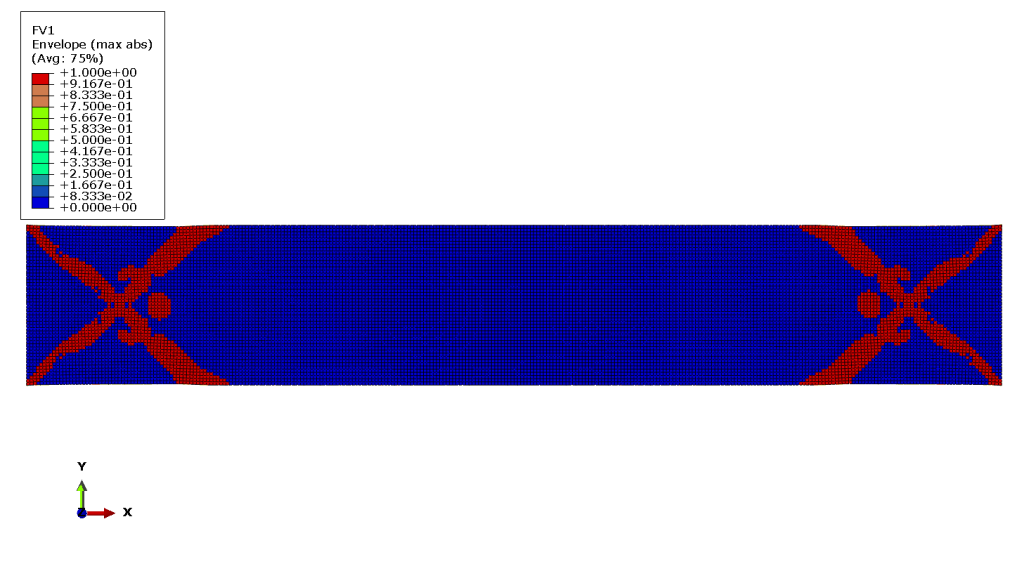
In-plan shear nonlinearity effect
Experimental observations have shown that composite laminates exhibit nonlinear and irreversible shear behavior, which is attributed to factors such as plasticity, progressive damage, matrix cracking, and fiber/matrix interfacial failure. These mechanisms lead to stiffness degradation and eventual catastrophic failure through fiber breakage.
The nonlinear shear behavior is typically described using an equation derived by fitting experimental data of shear modulus reduction. The constants in the equation are determined through static tension tests on specific laminate configurations, such as the [45/-45]_s orientation.
Exponential and polynomial functions are commonly employed to fit the nonlinear stress-strain behavior of materials. While polynomial functions can generally fit the stress-strain curve of most materials, higher-order functions may be necessary for special cases.
In modern structures, most laminated composites exhibit nonlinearity even under elastic conditions. This effect is particularly evident in plane shear experiments, where the stress-strain curve appears nonlinear even at low loads. Such experiments demonstrate a decrease in shear modulus as shear stress and strain increase.
According to ASTM D3518, the shear strength values are determined based on the shear stress corresponding to a shear strain of 5%. It is important to note that reaching this shear strain does not necessarily result in catastrophic failure of the specimen. However, at high shear strain values, the fiber alignment of the specimen may deviate from the nominal +-45 orientation. Therefore, the shear failure strain is considered to be equal to 5% in this context.
USDFLD and VUSDFLD user subroutines
The USDFLD and VUSDFLD are user subroutines in Abaqus that allow you to define additional field variables and their evolution equations during a finite element analysis. These subroutines provide a way to incorporate user-defined material behavior, element properties, or other customized field variables into your Abaqus simulation.
Both subroutines must be implemented in a user subroutine file written in a programming language compatible with Abaqus, such as Fortran (*.for or *.f) or C/C++. The subroutine files must be compiled and linked with the Abaqus software to be utilized.
The implementation of USDFLD and VUSDFLD requires a good understanding of the material behavior or field variable you want to define, as well as the underlying programming language. The Abaqus documentation provides detailed information, guidelines, and examples on how to implement and use these user subroutines effectively.
It is important to note that the usage of user subroutines requires careful development, verification, and validation to ensure accuracy and consistency with the intended behavior. It is recommended to consult the Abaqus documentation, including the “Abaqus User Subroutines Reference Manual,” and seek assistance from Abaqus support or online communities for further guidance and specific examples related to your application.
BanuMusa R&D is an expert in the development of Abaqus user subroutines. You can see products related to material damage subroutines below. Contact us for more information and consulting.
-
Product on saleAdvanced Failure Analysis of Composite Materials with Abaqus and Autodesk Helius PFA: A Comprehensive GuideOriginal price was: $ 550.00.$ 499.00Current price is: $ 499.00.
-
Fortran for Abaqus Subroutine$ 255.00
-
Abaqus VUMAT JHB and JH-2 Ceramic Model$ 199.00
-
Product on sale3D Hashin USDFLD Subroutine Failure Criteria for AbaqusOriginal price was: $ 124.00.$ 119.00Current price is: $ 119.00.
-
3D Hashin VUMAT Subroutine for Abaqus with Exponential Damage Evolution$ 455.00
-
Product on saleVUMAT Subroutine: Shear Anisotropic Modified GTN Damage ModelOriginal price was: $ 535.00.$ 490.00Current price is: $ 490.00.
-
Porous Elastomers Abaqus UHYPER Subroutine$ 55.00
-
Product on saleAbaqus Tutorial: LaRC05 Failure Criterion For Fiber-Reinforced CompositesOriginal price was: $ 110.00.$ 99.00Current price is: $ 99.00.