Abaqus CDP Model Issues for Fire Analysis
What is fire analysis in Abaqus?
1- Fire Design Code (Design of Concrete Structures)
The Fire Design Code Eurocode, also known as EN 1991-1-2, is a European standard that provides guidance on the design of structures to withstand the effects of fire.
Eurocode 2 design of concrete structures is one of the most common codes for designing and calculating concrete structures. Based on this code, the tensile and compressive strength of concrete decreases with increasing temperature. This decrease in strength is specified by a coefficient called the reduction factor.
These coefficients are non-zero for compressive behavior up to 1000 °C and for tensile behavior up to 500 °C. To simulate this property reduction in Abaqus software, one way is to use the CDP model. but the Abaqus CDP model issues at high temperatures! so how to overcome it?! Continue reading…
2- CDP Material Model
The CDP material model has the advantage of introducing the stress-strain behavior of concrete in compressive and tensile states and it can be dependent on temperature. Therefore, it is favorable for our thermomechanical fire analysis. Now stress-strain data must be entered into the CDP model for the compression and tension branches.
Also, when using the concrete damaged plasticity model in Abaqus, numerical problems may occur if the tensile strain of concrete has a small value.
Defining strain for the tensile behavior of concrete comparable to the reinforcement strain is shown to be of neglectable importance. but the problem is that for thermomechanical analysis at high temperatures such as 1000 °C, concrete completely loses its tensile properties at a temperature of 600 °C. This is where the issue of divergence usually occurs. I have explained the reason in detail in 3rd step.
3- Solving Abaqus CDP model issues
Although the design codes have not mandated the tensile strength of concrete, it is considered for a more accurate analysis of the elements at high temperatures and to predict their behavior. Also, when using the CDP model, we have to input concrete tensile behavior data.
The Abaqus has a default setting regarding the decreasing branches for tensile and compression branches. These intervals, tension stiffening and compression hardening respectively, are limited by a value of 0.01 of the maximum values on each branch. These values are reasonable and of less importance if the analysis is performed for ambient temperature.
Although not specifically mentioned in the software documentation, the constraint of a minimum of 1% is also related to the decrease of mechanical properties due to temperature. It can be noticed in Figure 3.2 of EN 1992-1-2 that compressive strength at high temperature is not decreasing below 1% of the ambient compressive strength.
The discussion is made on the tensile strength of concrete for high temperatures. Starting from 600 °C the concrete is considered to completely lose the tensile strength. Since Abaqus is set by default to consider a minimum value for the tensile strength, it is important to assess its influence.
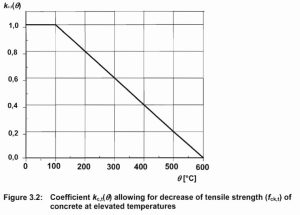
EN 1992-1-2 Reduction coefficient for tensile strength of concrete at elevated temperature
Now, to solve numerical issues in Abaqus, it is sufficient to use a coefficient close to zero, such as 0.01, instead of zero reduction coefficients at temperatures above 500 degrees. This will introduce a very small error in the analysis, which is negligible, but the analysis will be complete. You can calculate the error of this analysis for a small model.
Also, you may like this product…
Mastering Concrete Modeling in Abaqus: A Comprehensive Course
In the “Concrete Modeling in Abaqus” tutorial video course, we have tried to cover all the tips and tricks the user requires when modeling concrete structures. Material models are available in the Abaqus and their parameters are described. Also, the modeling methods of rebars and reinforcements are expressed one by one and the strengths and…