Essentially Abaqus Plug-in utilities (Add-ons) for Abaqus users – Part I
Table of Contents
Toggle1. Stress-strain Curve Calculator plug-in
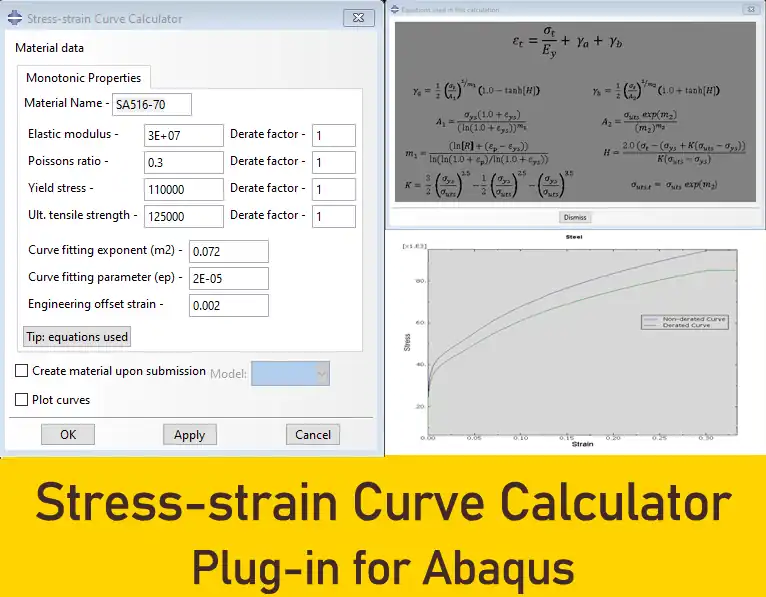
The Stress-Strain Curve Calculator is an Abaqus/CAE plugin that allows an Abaqus/CAE user to generate a stress-strain hardening curve applicable to design and fitness-for-service assessments (FFS- level 3) of pressure vessel and piping equipment. Plasticity hardening curves are often needed in the design and analysis of metallic components and structures. Elastic perfectly plastic and elastic bi-linear plastic models may not be adequate for all applications. This is particularly applicable when utilizing Design-by-Analysis methods described in ASME Section VIII Div. 2 documents for the design of pressure vessels and piping components or utilizing the ASME/API 579 Fitness-for-Service (FFS) document for assessing a pressurized component with a flaw.
2. Calibrate Nitinol Material Behavior plug-in
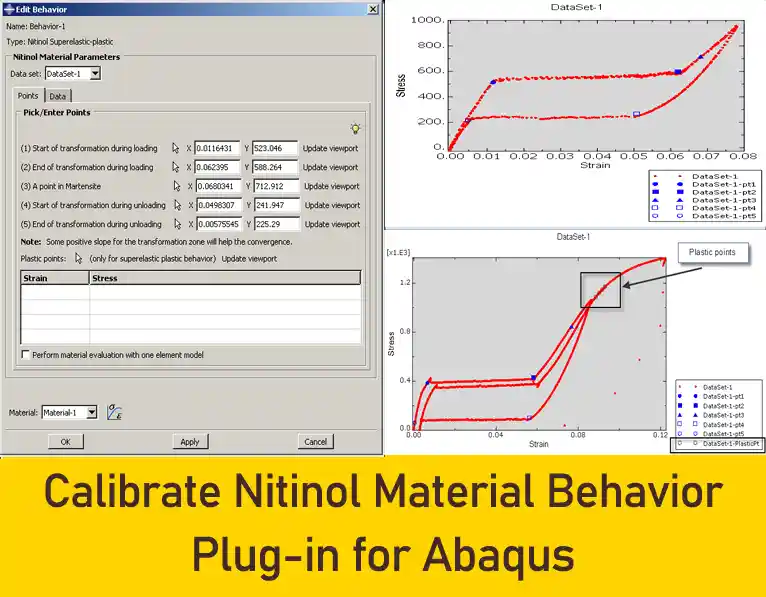
The Calibrate Nitinol Material Behavior plug-in is used for calibrating the superelastic & the superelastic-plastic behaviors of Nitinol for Abaqus/Standard or Abaqus/Explicit analyses.
The plug-in provides a user-friendly interface to create Nitinol material parameters based on uniaxial tension test data. Necessary keywords and data lines will be generated automatically based on a few characteristic points selected from the test data. The material will be renamed according to the required naming convention for Nitinol and can be directly used inside Abaqus/CAE. In addition, the Calibrate Nitinol Material Behavior plug-in offers an option to evaluate the material definition with a uniaxial 3D one-element model. If you select this option, the plug-in submits the analysis and plots the results with the original test data for comparison. You can iterate the above process by editing the points picked on the test data until the desired material behavior is achieved.
3. Creep Evaluation Plug-in Utility
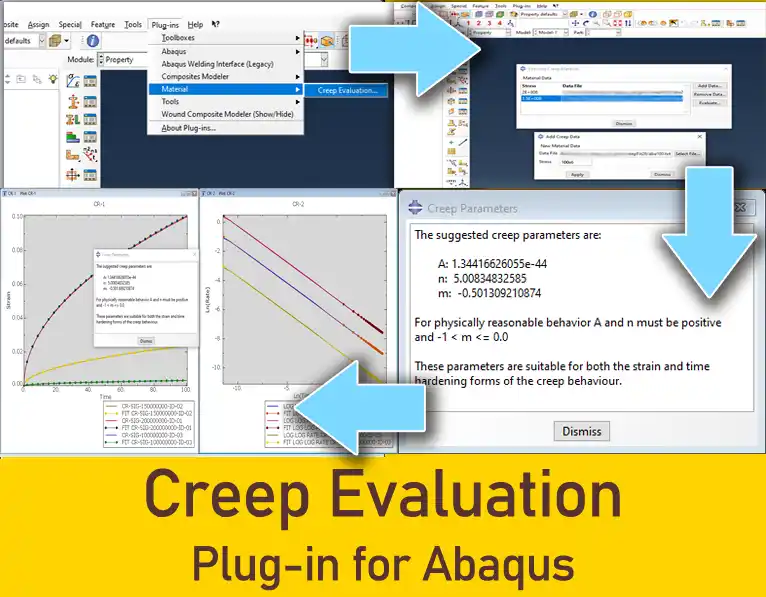
Creep Evaluation plug-in utility was very effective to me. Before that, I had to use a lot of code in MATLAB and Excel to calibrate and evaluate the creep constants.
It is similar to the Hyperelastic material evaluation tool within Abaqus/CAE – but for creep properties. The user must supply experimental data from a uniaxial creep test.
The Creep Evaluation plugin uses a least-squares technique to evaluate the constants that are appropriate for both the time and strain hardening forms of the creep relationship.
This plugin will allow you to evaluate the material constants for either the time or strain power-law creep, model. The user supplies material data (time, against creep strain) taken for different stresses.
4. MatLib (Abaqus Material Library) Plug-in
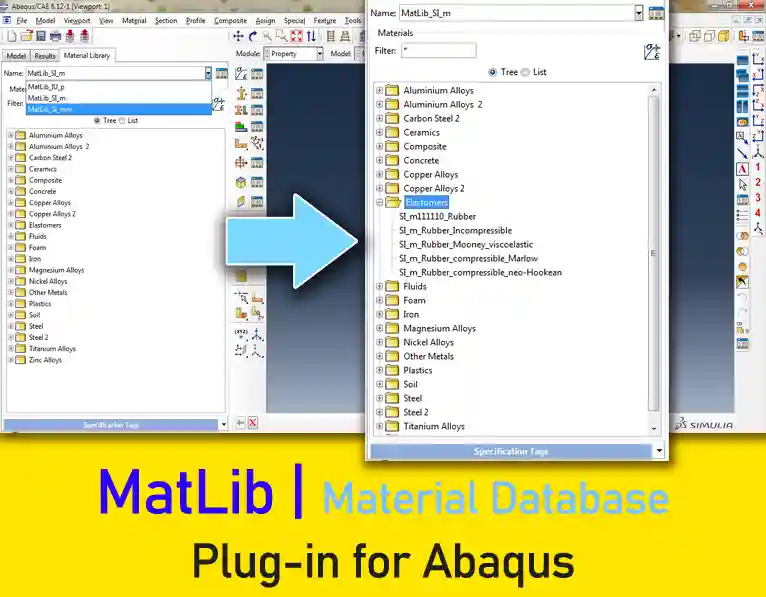
Having a library of materials with ready-made parameters helps a lot to accelerate and increase the accuracy of modeling and analysis in Abaqus. MatLib is a powerful library with more than 1400 materials in 22 groups such as composites, polymers, metals, etc. that have different models of materials such as elastic, plastic, damage, temperature and strain rate dependent, and many other specifications. The library is available in 3 units SI, SI (mm) metric, & Imperial. The plugin is developed by the Banu Musa simulation company.
5. Micromechanics Plug-in
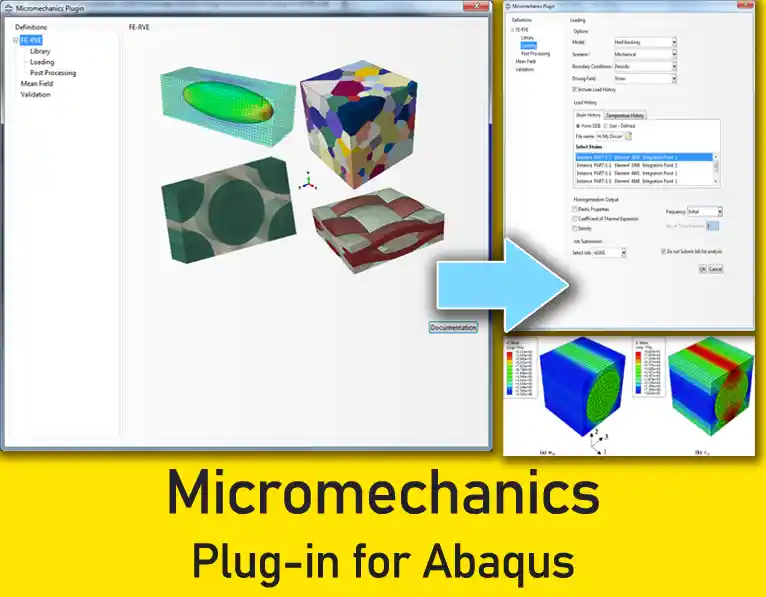
Micromechanics plugin has been developed for Abaqus/CAE that facilitates the setup, analysis, and post-processing of finite element representative volume element (FE-RVE) models. Such models permit a detailed study of the behavior of small-scale material microstructures under the influence of far-field loading.
Capabilities:
- Metal grain models
- Chopped-fiber
- Lattice Structures
- Validate Mean-Field Homogenization
- Constituent Property Prediction
- RVE Libraries
- RVE Boundary Conditions
- Periodic Boundary Conditions
- Homogenization – Calculating Elastic Response
- Solid-To-Shell Homogenization
- Homogenization – Stiffness Matrix
6. Wound Composite Modeler Plug-in for Abaqus
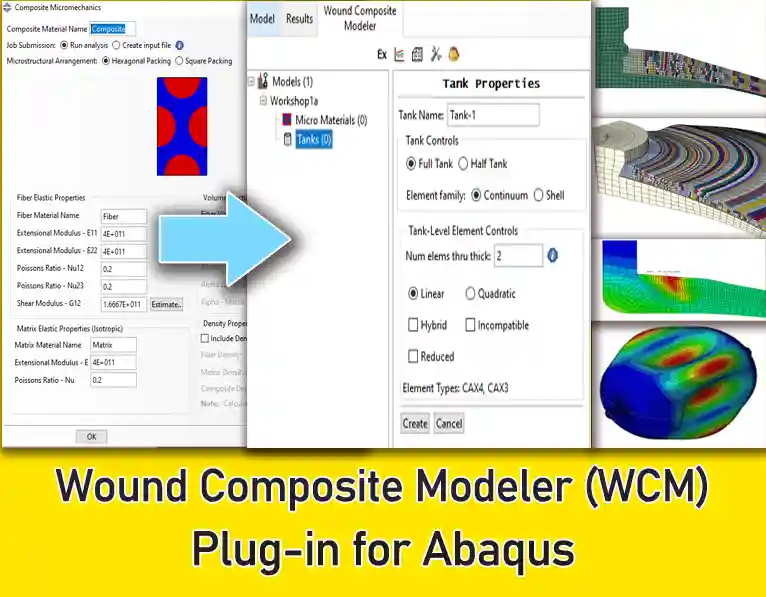
The Wound Composite Modeler (WCM) plug-in allows the user to define all the necessary information to create, analyze, and post-process a finite element model of a wound composite pressure vessel. The WCM plug-in applies a symmetry boundary condition at the mid-length point of the cylinder so that a half-symmetric model of the complete pressure vessel is created. If a given tank design has different end dome geometries, it can be analyzed by creating two separate models, one for each end of the vessel.
Analysis Approach
- Dome and Cylinder Geometry Definition
- Winding Layout Specification
- Mesh and Section Creation
- Loading
- Output
- Results
Including 5 workshops:
- Workshop 1: Generating Axisymmetric COPV Models
- Workshop 2: Generating 3D COPV Models
- Workshop 3: Autofrettage Analysis
- Workshop 4: Design
- Workshop 5: Buckling and Debonding
7. Johnson-Cook Constants Plug-in
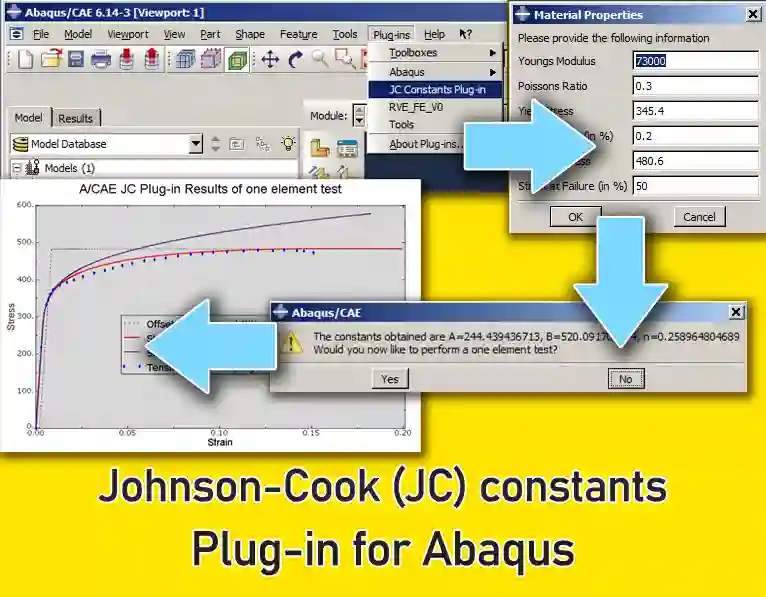
In Abaqus, there is a material model named Johnson-Cook. Johnson-Cook constants plugin has been developed to evaluate its parameters. In this way, the parameters related to this material model can be easily found without referring to handbooks and papers.
8. Autodesk Helius PFA
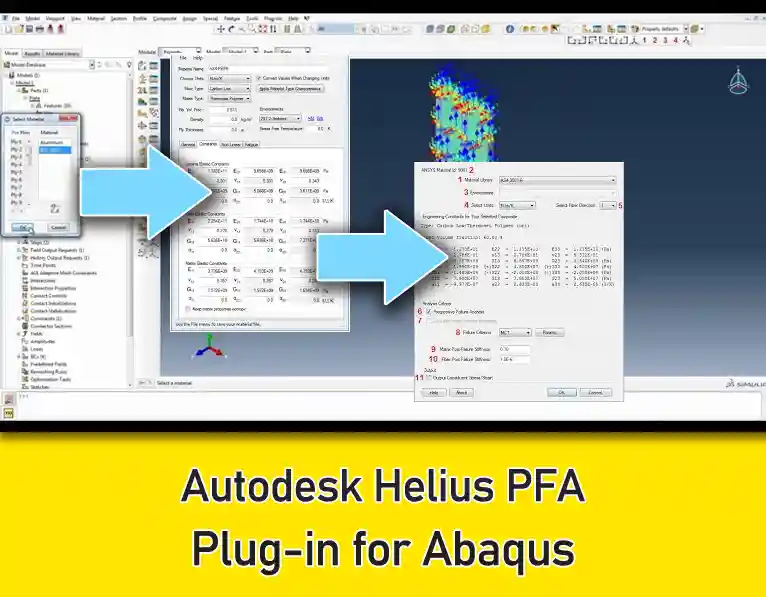
Helius PFA plugin is a good plugin to simulate the damage of composite materials that I personally have good experience with. With the Helius PFA plugin, it is possible to predict the dynamic failure and fatigue of composite materials, which is a non-motivational feature and can be used in addition to Abaqus in Ansys.
9. Bolt Studio Plug-in for Abaqus
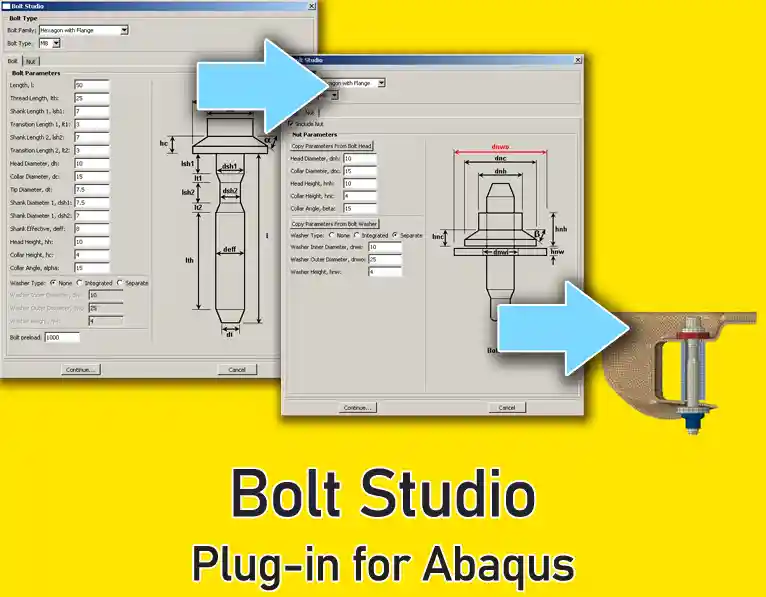
The Bolt Studio plug-in provides the user with a streamlined method for defining bolts, nuts, and washers and placing them into an existing Abaqus/CAE model. Users can control the default set of bolts that are displayed in the interface via a simple Python-based configuration file.
The bolts, nuts, and washers, where applicable, are generated parametrically within Abaqus/CAE and meshed automatically using a hexahedral mesh.
The mesh size is determined automatically based on the dimensions of the bolt (the user can re-mesh if required, the parts using the native meshing tools within Abaqus/CAE). The bolt is automatically partitioned and the user-specified pre-loading is applied.
10. Focused Mesh Contour Integral Crack Builder Plug-in
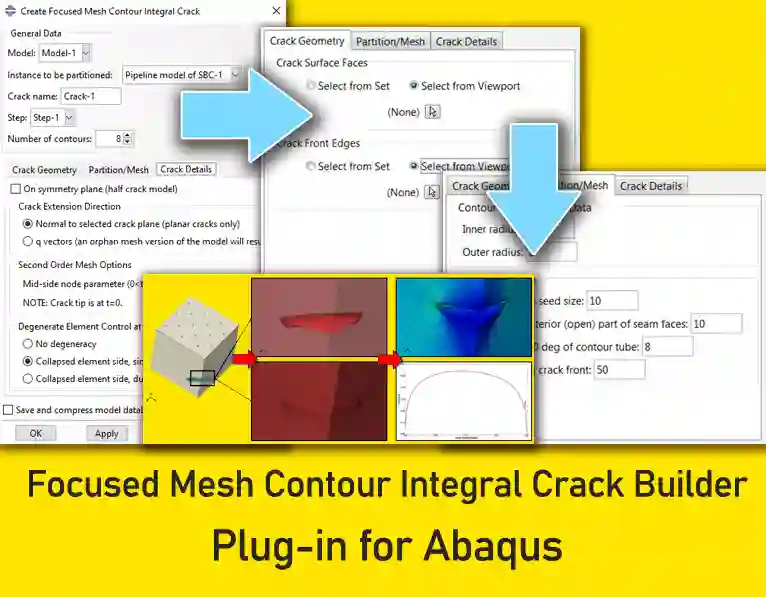
For many years Abaqus/Standard has included the ability to assess quasi-static, stationary crack fracture mechanics problems using contour integrals. While an XFEM-based contour integral method has been added in recent years, the conventional approach involves constructing a specific “focused” mesh configuration at the tip of the presumed crack. The Focused Mesh Contour Integral (FMCI) Crack Builder is an Abaqus/CAE plug-in to automatically create focused mesh partitions, meshes, and contour integrals (including q-vectors) for conventional focused mesh contour integral fracture analysis
11. ROMAC Bearing Plug-in
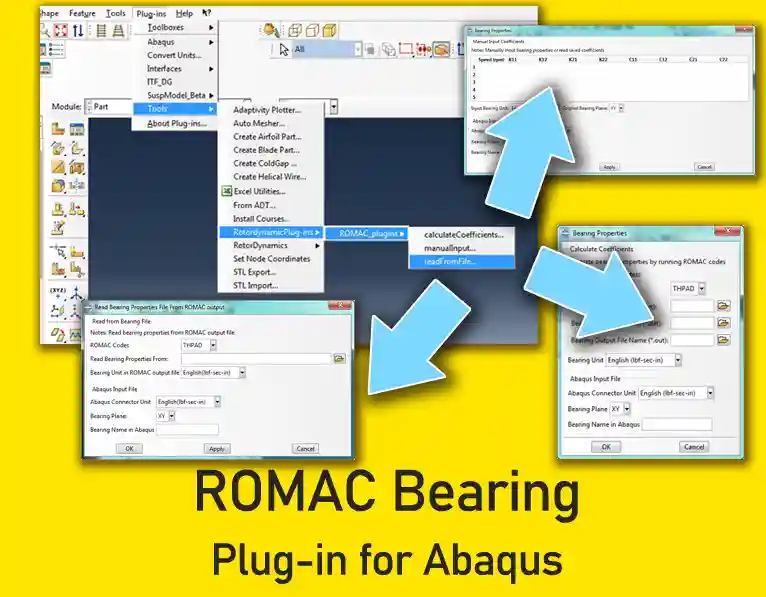
ROMAC bearing code is one of the popular bearing codes used in the Rotordynamics field. It is developed by ROMAC Laboratory at the University of Virginia. With ROMAC bearing plug-in you can perform rotor dynamics analyses easily with the bearing property information given by the ROMAC bearing code.
ROMAC bearing plug-in is useful to import the bearing properties from the ROMAC bearing codes THPAD, THBRG, and MAXBRG and write those in Abaqus input format. You can also fill out the bearing properties manually and write them in Abaqus input format using this plug-in.
The Abaqus input file .inp (which contains the properties of the connector element of the bearing with a given bearing name), is created using the plug-in. You can use the created properties in the proper connector element in your own model.
Three separate plug-ins allow for three different approaches to entering the bearing properties:
- Calculate Coefficients
- Manual Input
- Read from File
The Calculate Coefficients plug-in directly runs the ROMAC bearing software (THPAD or THBRG) and writes the bearing properties in an Abaqus input file. The output file name is set as *.inp using the bearing name which is assigned in the plug-in by default, after importing the bearing results. You must have the ROMAC bearing software (THPAD or THBRG).
The Manual Input plug-in allows you to enter the bearing properties manually and write them to an Abaqus input file.
The Read from File plug-in reads the ROMAC bearing output file and writes the bearing properties in an Abaqus input file.
Notes:
- By default, ROMAC uses English units. The plug-in can convert it to SI units.
- For uncoupled property, there is no version limitation. But for coupled property, only Abaqus 6.12 and later is available.
12. Units Converter Plug-in
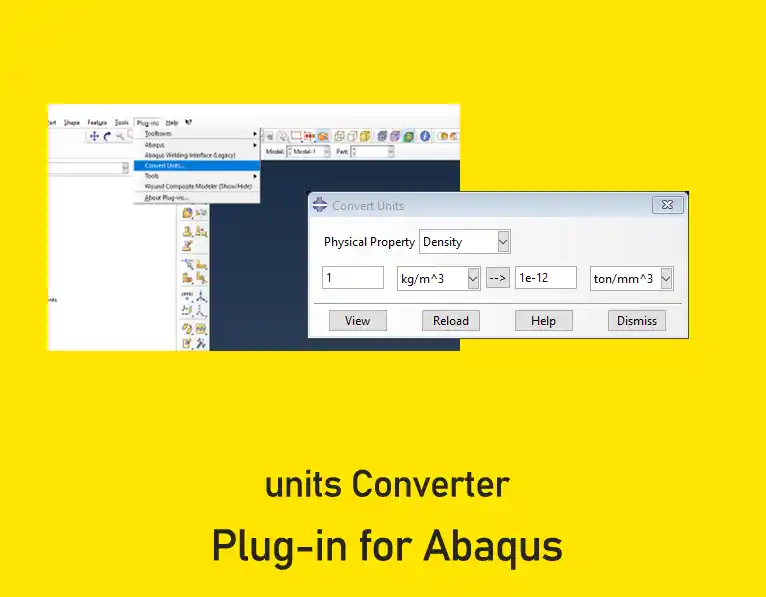
Units Converter plug-in is a handy tool for converting common units within ABAQUS/CAE. It was developed by James Lockley in 2005. Units are converted from one measurement system to another system. You can also develop your own unit system. It is very useful.
13. Abaqus Welding Interface (AWI) plug-in
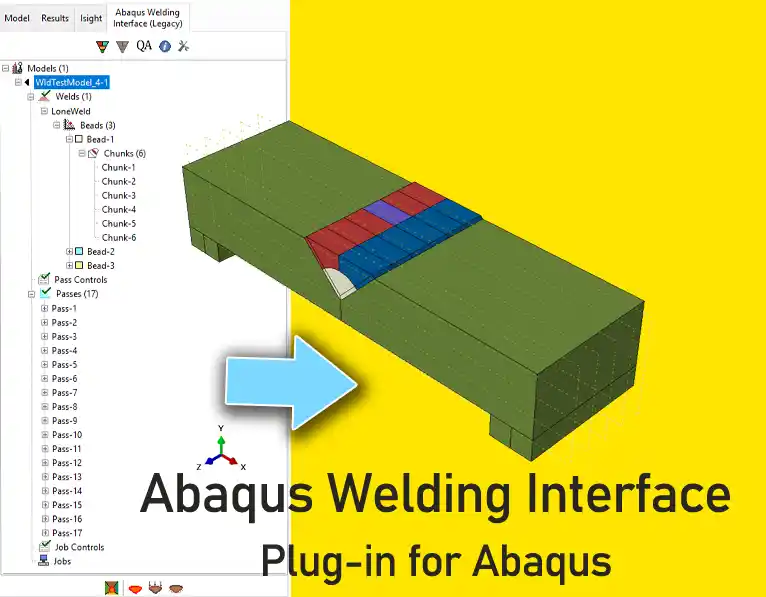
The Abaqus Welding Interface (AWI) plug-in streamlines the generation of two and three-dimensional welding simulations from within Abaqus/CAE. This application provides a model-tree-based approach to defining all aspects of the weld model such as weld beads, weld passes, film loads, and radiation.
14. Honeycomb Modeler plug-in
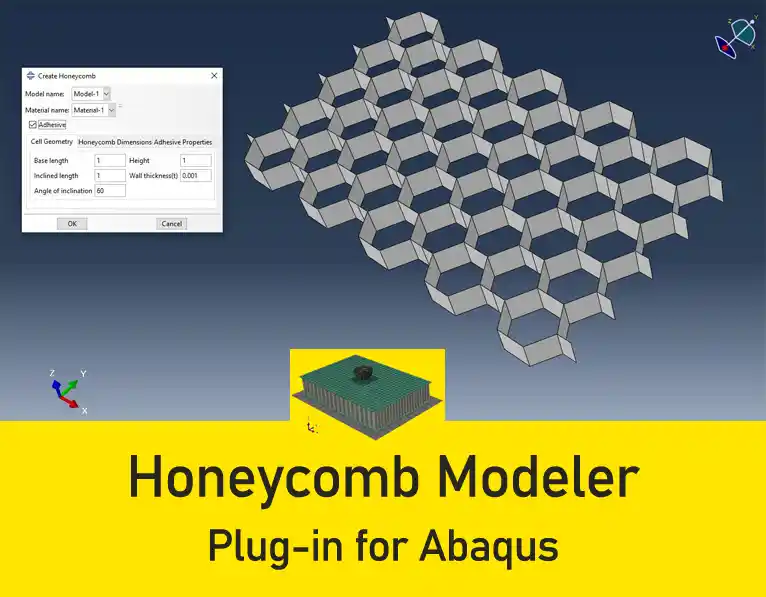
The Honeycomb Modeler plug-in can be used with any model included in an Abaqus/CAE database. It automatically creates honeycomb structure models. The honeycomb structure is described in the plug-in by its:
- material;
- unit cell geometry; and
- dimensions.
Any material that has been created in the model can be accessed from within the plug-in. In addition, new material can be conveniently created from within the plug-in by calling the material editor.
Working with the plugin is very simple and enjoyable. A lot of time spent on the geometric modeling of a honeycomb is minimized with this plugin. I recommend any Abaqus user have the Honeycomb Modeler plug-in for simulation.