Fitness-for-Service Analysis with Signal FFS Course
Fitness-for-Service Analysis with Signal FFS Course is designed to provide participants with a comprehensive understanding of how to assess the fitness of equipment using API-579/ASME FFS-1 and BS 7910 methods, specifically focusing on the evaluation of equipment with various flaws. Throughout this training, you will delve into both the theoretical framework and practical application of FFS assessments, utilizing specialized procedures tailored for pressurized equipment. By the end of this course, you will gain valuable insights into conducting FFS evaluations and solving example problems using manual calculations and Signal FFS software.
What is FFS?
Fitness-for-Service (FFS) assessment involves a comprehensive method that assesses structural elements to ascertain their suitability for ongoing use.
This course is structured with lectures, demonstrations, and workshops. The workshops are crucial for the training as they aim to solidify the ideas covered in the lectures and demonstrations. Their purpose is to give participants hands-on experience in conducting and troubleshooting real FFS analyses.
Signal FFS
Signal FFS is a comprehensive software package designed for Fitness-For-Service evaluation and fracture mechanics analysis. It conducts assessments following the API 579-1/ASME FFS-1 2016 standard and the British Standard BS 7910. The software simplifies the evaluation of pitting, corrosion, brittle fracture, dents, laminations, hydrogen damage, and crack-like flaws in various components.
Signal FFS features extensive databases of material properties for fatigue crack propagation and creep rupture. For fatigue crack propagation, users can choose between the NASGRO database for nearly 500 different metallic materials (List of materials), which contains material constants for fatigue crack growth analysis published by NASA, and BS 7910 material constants. Material constants for creep analysis are based on the MPC Materials Properties Council Omega method and sourced from API 579 Appendix F.
The software offers an intuitive Windows™ interface for easy navigation. It is important to note that Signal Fitness-For-Service is tailored for competent engineers with a solid understanding of fracture mechanics and Fitness-For-Service methodology.
Signal FFS software allows users to conduct assessments varying from basic Level 1 to more detailed Level 2 and advanced Level 3 evaluations of remaining life.
FFS Assessments
The API 579/ASME FFS-1 Fitness-For-Service method defines three assessment levels. If Level 1 criteria aren’t met, a repair or Level 2 assessment is needed. If Level 2 criteria aren’t met, a repair/replacement or Level 3 assessment is necessary. The higher the level, the more information and experience the assessing engineer needs.
Level 1: Basic inspection data and a screening curve, can be done by a plant inspector or engineer.
Level 2: Less conservative than Level 1, requires detailed data and more complex calculations, must be done by a plant engineer or specialized engineer.
Level 3: Requires a highly experienced engineer due to advanced analysis and judgment, may involve stress analysis or complex finite element analyses, sometimes leading to repair or replacement.
What you’ll learn
In this Signal FFS course, you will learn about FFS Analysis using Signal FFS, and FFS assessment using API579 and BS 7910.
Upon successfully finishing this course, every participant will have the ability to:
- Present various damage mechanisms, their causes, and prevention methods.
- Examine damage mechanisms and stress the importance of identification.
- Explore the sections of API 579-1/ASME FFS-1 2016 and BS 7910 that are utilized for evaluating brittle fracture, crack-like defects, corrosion, and creep.
Comprehend and apply foundational knowledge on an FFS assessment. - Analyze, assess, and supervise pressurized equipment for ongoing operation.
- Resolve sample problems (over 60) demonstrating the practical use of the techniques in API 579-1/ASME FFS-1 2016.
- Discuss the correlation between API 579-1/ASME FFS-1 2016 and BS 7910 standards.
- Provide an overview of remaining life assessment, remediation, and methods to prolong the lifespan of damaged equipment.
As part of the course, The API 579 and BS 7910 standards will be available, at no cost.
Overview of the course
Lecture 1 Introduction to Fitness-for-Service
- ASME/API-579 Fitness-for-Service (FFS) Overview
- BS 79 10 Overview
- Scope and Objectives
- FFS assessment procedures
- Responsibilities in FFS
Lecture 2 FFS Methods and Margins
- Design Margins for New Equipment
- Remaining Strength Factor
- Margins for In-Service Equipment
- Three Levels of FFS Analysis
Lecture 3 Introduction to Signal FFS
- Assessment Methodologies
- Analysis
- Supported equipment types
- Units
- Analysis type
- Assessments
- Design
- Design codes
- Component types
- Design pressure and temperature
- Flaw details
- Assessment location
- Materials
- Material databases
- Material specification
- Material grade
- Material group
- Allowable stress
- Dimensions
- Loads
- Operating conditions
- Hydrotest pressure
- Impact test temperature
- Parametric and Monte Carlo Analyses
- Parametric Analysis
- Monte Carlo FAD Analysis
- Run and results
- Reports, curves, and figures
Lecture 4 Brittle Fracture
- Factors Influencing Brittle Fracture
- Applicability and Limitations
- Data Requirements
- Level 1 and 2 Brittle Fracture Assessment
- Workshop Butt Welded Components of Pressure Vessel
Lecture 5 General Metal Loss
- Local vs General Thinning
- Applicability and Limitations
- Data Requirements
- Level 1 and 2 Assessment
- Remaining Life Assessment
- Workshop General Metal Loss of Pressure Vessel
Lecture 6 Local Metal Loss and Groove-Like Flaws
- Applicability and Limitations
- Data Requirements
- Level 1 and 2 Assessment
- Remaining Life Assessment
- Remediation
- Workshop Local Thin Metal Loss of Pressure Vessel
- Workshop Groove-Like Flaw of Pressure Vessel
Lecture 7 Pitting Corrosion
- Applicability and Limitations
- Pit Measurement and Pit Couples
- Level 1 and 2 Assessment
- Remaining Life Assessment
- Remediation
- Workshop Pitting of Pressure Vessel
- Workshop Pitting with Local Thinning of Pressure Vessel
Lecture 8 Hydrogen Damage
- Applicability and Limitations
- Inspection Technique and Sizing Requirements
- Data Requirements
- Level 1 and 2 Assessment for Blisters, HIC and SOHIC
- Remaining Life Assessment
- Remediation
- Workshop Hydrogen damage of Pressure vessel
Lecture 9 Weld Misalignment and Shell Distortion
- Applicability and Limitations
- Data Requirements
- Level 1 and 2 Assessment
- Remaining Life Assessment
- Remediation
Lecture 10 Crack-Like Flaws
- Applicability and Limitations
- Flaw Sizing and Inspection Technique
- Level 1 and 2 Assessment
- Failure Assessment Diagram (FAD)
- Leak before Break
- Remediation and In-Service Monitoring
- Workshop Cracking of Cylinder
- Workshop Cracking of Sphere
- Workshop Fatigue Plate with Hole Corner Crack Grow to final depth
- Workshop fatigue Flat Plate Surface Crack Grow to Failure
Lecture 11 High Temperature Creep
- Applicability and Limitation
- Data Requirement
- Assessment Technique
- Creep Rupture Life for Tubes
- Remediation
- Workshop Creep of Cylindrical Shell
- Workshop Average Larson-Miller Creep Parameters for a tube
Lecture 12 Assessment of Dents, Gouges and Dent-Gouge Combinations
- Applicability and Limitation
- Data Requirement
- Level 1 and 2 Assessment of Dents Only and Gouges Only
- Level 1 and 2 Assessment of Dents and Gouge Combination
- Remaining Life Assessment
- Remediation
- Workshop Dents of a Pipe
Lecture 13 Assessment of Lamination
- Applicability and Limitations
- Data Requirements
- Level 1 and 2 Assessment
- Remaining Life Assessment
- Remediation
- Workshop Lamination in a Pressure Vessel
Knowledge Prerequisites
This course is recommended for engineers with experience in FEM.
Who Should Attend
This course targets engineers and engineering managers involved in operating, designing, analyzing, and maintaining plant facilities. Participants should possess a Bachelor of Science degree or equivalent engineering experience. A basic understanding of stress analysis, materials behavior, and fracture mechanics is advantageous.
This course is available offline with 24/7 online support.
A certificate of completion will be provided to participants who successfully attend and finish the course.
Targeted Audience
- Integrity Assessment Engineers
- Maintenance Engineers
- Site Inspection Engineers
- Piping Engineers
- Mechanical Engineers
- Plant Engineers
- Fixed–Equipment Reliability Engineers
- Simulation Analysts
- FFS Engineers
- Welding Engineers
- Operational Personnel
- Process Engineers
- Project Managers
- HSEQ Personnel
Available Releases
Signal FFS Version 5.1
Duration
10 hours
Discipline
Fitness-for-Service Analysis with Signal FFS Course is designed to cover the utilization of the Signal FFS for level 1, 2, and 3 FFS analysis. It is aimed at engineers involved in FFS assessment who wish to enhance their comprehension of the intricate mechanical and failure behavior associated with plant facilities.
Need help? Get a consultation from our experts.
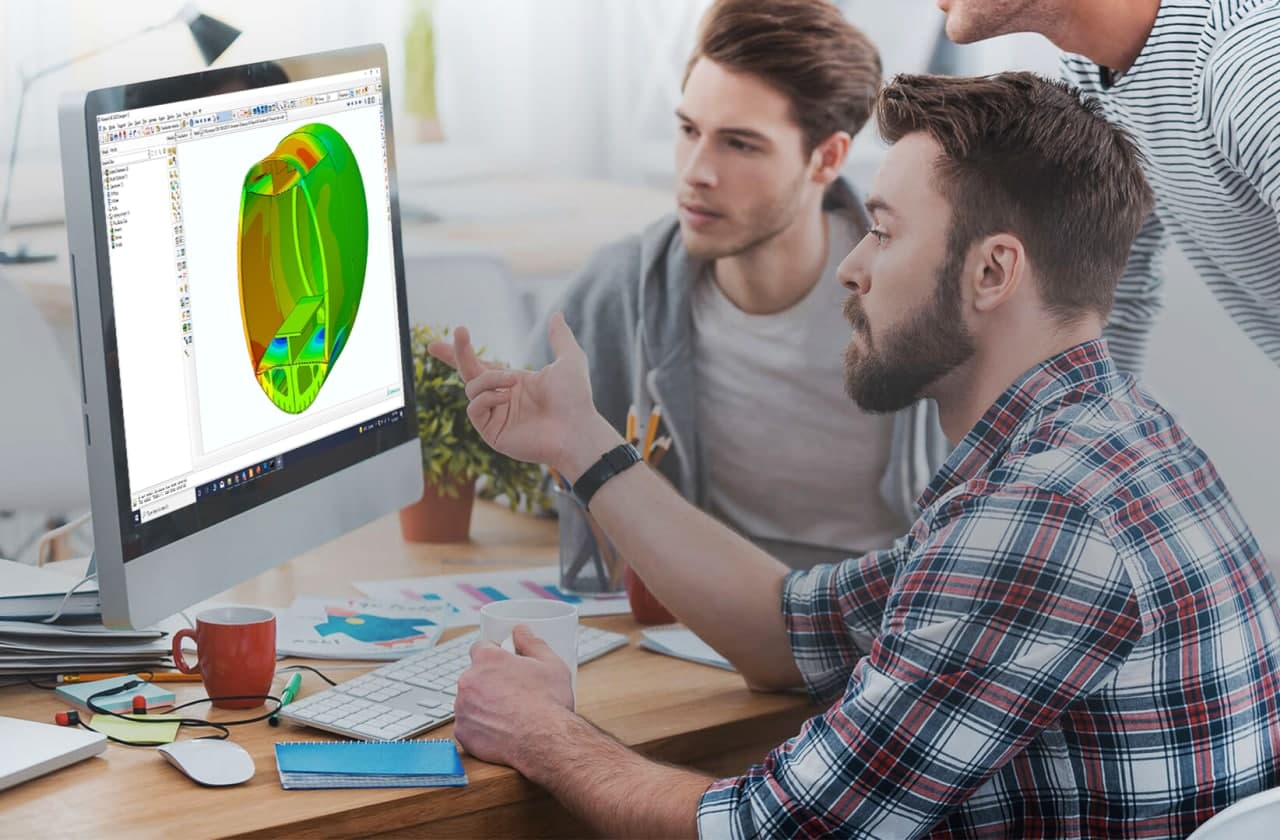
Telegram: +98-915-55-20-388
WhatsApp: +98-915-55-20-388
Find Us on WeChat
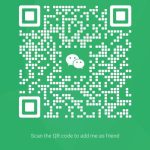
Reviews
There are no reviews yet.