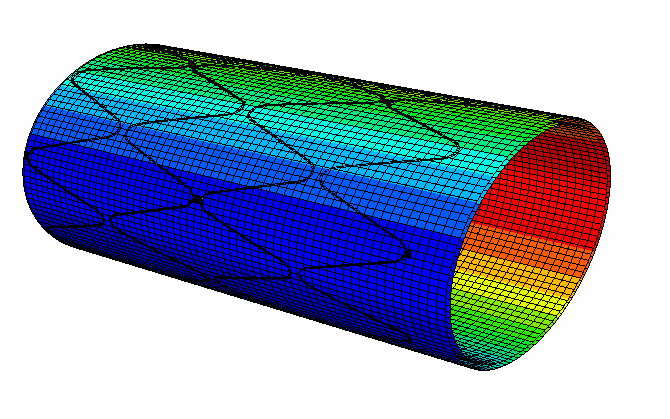
Cyclic Analysis of Axial Flow Valve Sleeve
In this project, cyclic analysis of axial flow valve sleeve was simulated using Abaqus FEA. The rubber sleeve is the only moving part of the axial flow valve in the gas pressure-reducing stations and at the same time, it has a unique and key function in the valve. The purpose of this simulation was to determine the life of a sleeve under cyclic loading. The material of this part was subjected to various tests and the optimal behavioral model was determined for it and the failure and fatigue behavior of this material under cyclic and static loading was investigated.
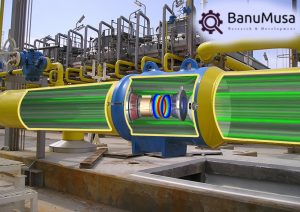
Cyclic analysis of axial flow valve sleeve in gas stations
Problem
One of the problems in gas pressure-reducing station regulators is sleeve failure. The rubber sleeve is subjected to cyclic loading during its life. This cyclic load is due to fluctuating gas pressure. The fluctuating load leads to a reduction in the life of the rubber sleeve and eventually, it needs to be replaced. Abaqus FEA modeling and simulation can help to better understand the behavior of this component under loading conditions.
Solution
We investigate the consequences of applying cyclic loading when the rubber exhibits a Mullins effect. The Abaqus Mullins effect is a dependence of the hyperelastic response on the maximum deformation previously experienced.
The Mullins effect describes how filled rubber elastomers exhibit stress softening under quasi-static cyclic loading.
The simulation results were reported as:
- Predicting the resistance of the part to cyclic load at high pressure
- Determining the best behavioral model for Hyperelastic rubber-like material
- Determine the remaining life of the elastomer sleeve under cyclic loading
- Analysis of failure and fatigue of Hyperelastic materials
- Predict the region of failure in the part
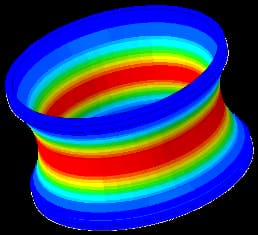
Displacement contour of the sleeve under cyclic loading
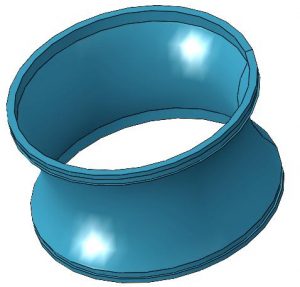
3D model of regulator sleeve
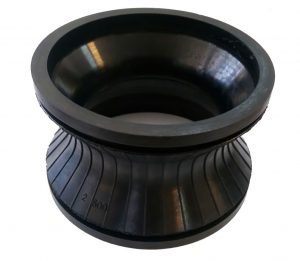
The axial flow valve sleeve