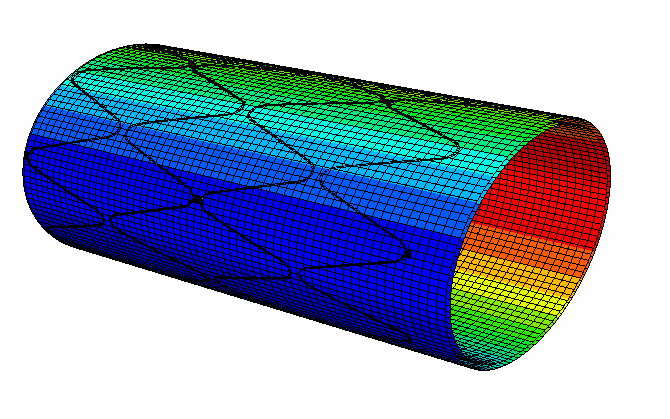
Progressive Damage Modeling Composite Laminates under Hypervelocity Impact Loading
Progressive damage modeling composite laminates under hypervelocity impact loading aims to:
- Predict the initiation and evolution of damage over time as the impact event progresses
- Account for different damage modes like fiber fractures, matrix cracks, delamination
- Model the reduction in material stiffness and strength as damage accumulates
- Consider interactions between different damage mechanisms
- Capture non-linear material response due to high strain rates and impact loads
Determining the impact resistance of composite structures is very important in the automotive, marine, and aerospace industries. In this project, the simulation of high-velocity impact, composite impact resistance, and ballistic limit of a composite structure with a specific lay-up and material were investigated and estimated.
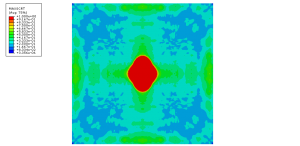
High-velocity impact simulation on composite structures
Hypervelocity Impact Simulation is important when the structure is crashed by a bullet or high-velocity object. In these cases, the ballistic limit of the material and structure is important. Famous examples are bulletproof jackets that must withstand bullets up to 800 m/s. In this research, high-velocity impact simulation was performed on a composite structure by finite element method (FEM) using Abaqus & LS Dyna.
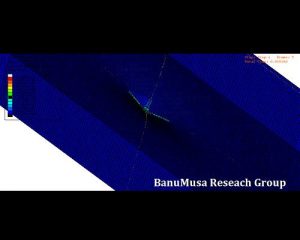
Progressive Damage Modeling Composite Laminates under Hypervelocity Impact Loading
The Purpose of Hypervelocity Impact Analysis
Hypervelocity impact simulation enables engineers to predict impact damage, assess residual performance, understand failure mechanisms, improve material models, optimize impact resistance, validate non-destructive techniques, reduce physical testing needs and perform “what-if” analysis – all of which help develop safer and more impact-resistant composite structures.
- Determination of residual strength of composite structures
- Determining the optimal layup & stacking sequence for laminate
- Determining the appropriate material and specifications for impact resistance and non-penetration of the projectile
- Determining the area and modes of failure with the help of Hashin, Puck, LaRC05, etc.
- Determining the ballistic limit of a composite structure
- Failure prediction and progressive damage analysis
- Investigation of the effect of projective geometry on penetration and its failure rate in the structure
high-velocity impact analysis FEA project
Hypervelocity Impact Simulation Achievements
- Fortran VUMAT subroutine can be used in Abaqus finite element software
- Can be used for multilayer and hybrid composites of any composite materials
- Usability for low and high velocity and includes strain rate effects
- Industrial and research application
- Complies with the proposed failure criteria
- Optimal code has high computational speed and accuracy
- Application in LS-Dyna and Abaqus software
- Includes Delamination mode
The results of progressive damage analysis enable engineers to optimize composite laminate designs for improved damage tolerance and performance.
History of Progressive Damage Modeling
The history of progressive damage modeling of composite laminates under hypervelocity impact loading has evolved in several stages:
Early models (1980s – 1990s):
- Initial damage models were developed that could predict basic failure modes like fiber fractures and matrix cracks.
- Models were able to capture damage initiation based on strength-based failure criteria.
- Models assumed brittle material behavior and did not consider damage evolution.
Improvements in material models (1990s – 2000s):
- Material models were developed that could account for stiffness degradation as damage accumulated.
- Damage evolution parameters like fracture toughness were included to model progressive damage.
- Nonlinear material behavior was captured to some extent, especially at high strain rates.
- Models were able to predict multiple damage modes and their interaction.
Experimental validation and refinement (2000s – 2010s):
- Experimental impact testing of composites at high velocities became more common.
- Simulation results could be validated against experimental data and model parameters refined.
- Multi-scale modeling approaches were developed that integrated micro-, meso- and macro-level mechanisms.
- Probabilistic and statistical methods were introduced to account for uncertainties and variability in materials.
Recent advances (Past decade):
- Material models have been developed specifically for hypervelocity impact loading conditions.
- Models can capture complex behavior due to shockwaves, wave propagation, and high strain rates.
- Advanced damage metrics have been proposed to better characterize damage evolution.
- Nondestructive inspection techniques have improved to validate predicted damage.
.You can call our expert right now for consulting.