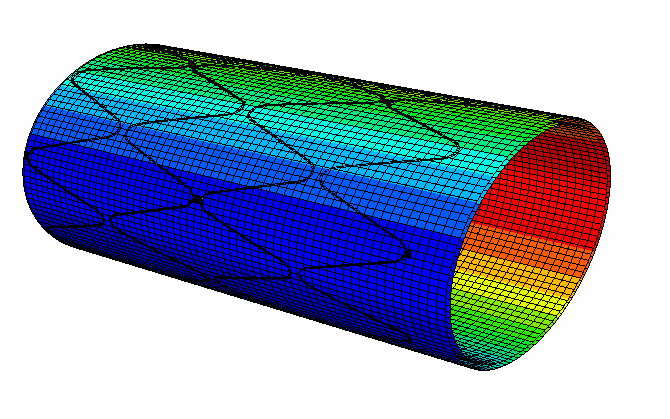
Deep Drawing Process
The deep drawing process, also known as “deep drawing” in manufacturing, is a cold-forming process used to convert flat metal sheets into three-dimensional shapes. In this process, a flat sheet is placed over a die and a punch pushes the sheet into a cavity of the die, forming the desired shape.
Deep drawing is commonly used in the manufacturing of metal parts such as pots, sinks, cans, automotive bodies, and more. It is an efficient and versatile process that allows for the production of parts with complex shapes from metal sheets.
One of the deep drawing process applications uses it to produce outstanding patterned sheets that are now widely used in manufacturing various devices. Patterned sheets are also widely used in the construction industry’s production and manufacture of metal doors. The production of kitchen sinks is also one of the most common applications of the deep drawing process.
Selection and design of die and punch presses
To perform the deep drawing process, press machines with different dimensions and sizes are needed, which are selected depending on the type and shape of the protrusion and depression, as well as the material and thickness of the material used. This process is carried out using a punch and die. The design of the die and punch, as well as the determination of the force required for forming, etc., are the prerequisites for the production of parts with a deep drawing process that must be calculated before production using engineering software.
Deep Drawing Process Analysis
By deep drawing process Simulation in CAE software like Abaqus, a lot of information can be obtained, some of which is as follows:
- Detailed simulation of complex mechanical behaviors, material properties, and interactions involved in the process.
- Can predict how materials will deform, stress distributions, and potential failure points during the process, helping to optimize designs and processes.
- Test different design variations and parameters without the need for physical prototypes, saving time and costs.
- Enabling engineers to understand and interpret the behavior of materials during the process.
- Feasibility study of part production
- Calculate the force required to produce the part
- Selecting a press machine to produce special parts
- Calculate the amount of spring back of the part after the process
- Calculate the required force of the sheet clamps
- Process optimization according to different conditions
- Calculate the stress distribution across the part
- Calculate the amount of wrinkling of the edges of the sheet
- Calculate the pressure required in hydraulic presses
- etc.