Bending Pipe Plugin for Abaqus
Wherever you are, if you are working on the pipe bending process, the Bending Pipe Plugin allows you to speed up the modeling process, and easily analyze and improve it with parametric facilities.
What is the pipe bending process?
Abaqus Bending Pipe Plugin
During the development of a product, it is important to know the feasibility of the product before the manufacturing stage. One of the activities covered by the metal forming process is the bending pipe process and it is critical, to save costs and time, a feasible design.
The bending pipe plugin for Abaqus is intended to cover this necessity, allowing the designer to assess the bending process easily and quickly.
The bending pipe plugin is completely parametrized for the circular sections and does not need expert knowledge about the bending process. The user to confirm the material and dimensions of the tube and tools. The plugin is divided into different steps, which help the user through model performance. The bending pipe plugin also implemented different methods of bending such as:
Classical Bending
Also named Rotary Draw Bending. It is the most typical bending method when you need to keep the original section of the pipe and reach complex geometries.
Compression Bending
It is similar to Classical Bending, but it is more simple and is not capable of making complex geometries.
Roll Bending
This method has roller components, which are continuously moving. It is suitable for long-bent radii.
Press Bending
The tooling in this method has the final shape of the pipe and is formed by press forces, like in the stamping process.
Stretch Bending
In this method, the pipe is subjected to tensile force, and the bent is done by rotating the pipe ends on a Die tool.
One Step
currently, this option only creates both meshes undeformed and deformed, which could be used with inverse analysis capability in Abaqus 2019 or higher.
Need help? Get a consultation from our experts.
Telegram: +98-915-55-20-388
WhatsApp: +98-915-55-20-388
Find Us on WeChat
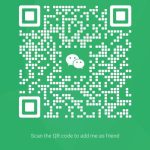
Reviews
There are no reviews yet.