Anisotropy Calculator Abaqus Plugin
Anisotropy Calculator ā Overview
Anisotropy in metals often arises during cold working due to the reorientation of their microstructure. Accurately defining this characteristic is crucial for improving the precision of results, particularly in simulations of sheet metal forming. For this purpose, obtaining reliable anisotropic parameters is essential. Various researchers, including Hill, Barlat, and Banabic, have developed mathematical models to describe anisotropic behavior. Some models are better suited for normal anisotropy, while others are optimal for planar anisotropy, with the chosen model significantly influencing the final simulation outcomes.
The Anisotropy Calculator plug-in (see Abaqus plugin database) simplifies calculating these parameters. It supports multiple established anisotropy laws, allowing users to calculate parameters using standard experimental data. The plug-in includes:
1. Banabic-2005
The Banabic-2005 criterion is a yield function that extends previous anisotropy models to provide a better fit for materials with complex anisotropic behavior, particularly for aluminum alloys. Developed by Dorel Banabic, this model is especially effective in describing anisotropy in automotive sheet metals, offering high accuracy in cases where other models might fall short.
2. Barlat-2005 (YLD-2004-18P)
Known as YLD2004-18p, this model by Barlat and co-authors is a sophisticated anisotropic yield criterion designed for aluminum alloy sheets. It offers a good balance between computational efficiency and accuracy in capturing complex anisotropy. The ā18Pā in the name refers to the 18 parameters that the model requires, making it flexible but complex. It is widely used in the automotive industry for materials that show strong directional dependency in their properties.
3. Barlat-89
The Barlat-1989 model, often called Barlat89, is one of the earlier anisotropic yield criteria and uses six parameters to represent anisotropy in metal sheets. This model is particularly well-suited for metals with a lower degree of anisotropy and was one of the first to improve upon earlier isotropic models, offering a more realistic representation of material behavior in sheet metal forming.
4. Barlat-91
- The Barlat-1991 criterion is an evolution of the Barlat-89 model and includes eight parameters to capture anisotropy in materials. It was created to better handle complex anisotropic behavior, especially in aluminum and steel sheets used in automotive applications. This model provides more accuracy than Barlat-89 in cases where additional detail is required.
5. Hill-48
- The Hill-1948 yield criterion, also known as Hill48, was one of the first widely accepted anisotropic models and has been commonly used for metals with a moderate degree of anisotropy. It uses a quadratic yield function that depends on a few parameters, making it easy to implement but less accurate for materials with high anisotropy. It is still used today for its simplicity and relatively low computational cost.
6. Hill-90
- The Hill-1990 criterion is an improvement over the Hill-48 model, incorporating additional parameters to capture anisotropic behaviors more accurately. This model is also quadratic and is used for materials with directional properties, like rolled sheets. It provides more flexibility than Hill-48 in capturing anisotropy in materials that have been processed to alter their grain structure.
7. Hill-93
The Hill-1993 criterion further refines Hill-90 by adding more parameters, allowing it to capture even more complex forms of anisotropy. Hill93 is especially useful for materials with very distinct directional dependencies and can be more computationally intensive than Hill-48 and Hill-90 due to its added complexity. It is suitable for advanced simulations in applications like automotive and aerospace, where material anisotropy plays a crucial role.
The Anisotropy Calculator makes selecting the most accurate model for each scenario easier, enabling more dependable simulation results for industrial applications.
- Easy Parameter Calculation: Users can input typical experimental data, and the plugin automatically calculates the corresponding anisotropic parameters, eliminating manual calculation and reducing error risk.
- Improved Simulation Accuracy: By leveraging accurate anisotropic parameters, this plugin enhances the precision of simulation results, which is especially critical in applications like sheet metal forming where directional properties impact material deformation.
Model | Developer | Primary Use Cases | Complexity (Parameters) | Key Application |
---|---|---|---|---|
Banabic-2005 | Banabic | Complex anisotropy (aluminum alloys) | Moderate | Automotive |
Barlat-2005 (YLD-2004-18P) | Barlat et al. | High anisotropy, especially aluminum | High (18 parameters) | Automotive |
Barlat-89 | Barlat | Low to moderate anisotropy | Low (6 parameters) | General metals |
Barlat-91 | Barlat | Complex anisotropy | Moderate (8 parameters) | Automotive |
Hill-48 | Hill | Moderate anisotropy | Low | General metals |
Hill-90 | Hill | Complex anisotropy | Moderate | Sheet forming |
Hill-93 | Hill | High anisotropy | High | Aerospace, automotive |
Anisotropic yield criteria
Anisotropic yield criteria are mathematical formulations that describe how materials yield (or start to deform plastically) when subjected to stresses in different directions. Each model was developed to address different types of anisotropic behaviors, commonly observed in metals due to cold working or rolling, which aligns their grain structure in specific directions.
Abaqus Workshops/ Examples
The plugin has 4 examples.
- Example:Ā Banabic-2005
- Example:Ā Barlat-2005 (YLD-2004-18P)
- Example:Ā Barlat-91
- Example:Ā Hill-48
Installing The Plugin
Extract the contents of the zip folder into a subdirectory of the abaqus_plugins folder, which can either be located in the
- abaqus_dircodepythonlibabaqus_plugins where abaqus_dir is the Abaqus parent directory or,
- home directory (in which case the plugin will be available whenever Abaqus is run) or,
- within the current working directory of your Abaqus/CAE session.
Compatibility
The Abaqus plugin is designed to be compatible with all Abaqus/CAE versions including Abaqus 24 and Python 3.
Updates
Version 2024
Who this plugin is for:
- Engineering or science students and professionals who work in the metal sheet forming
- Advanced students, Ph.D. students, or researchers for their Abaqus FEA projects
- Any Abaqus Application Engineer who is involved with various daily simulationĀ projects
What youāll gain
- You will be able to simulate and calibrate anisotropy metal material models in Abaqus in much less time.
Need help? Get a consultation from our experts.
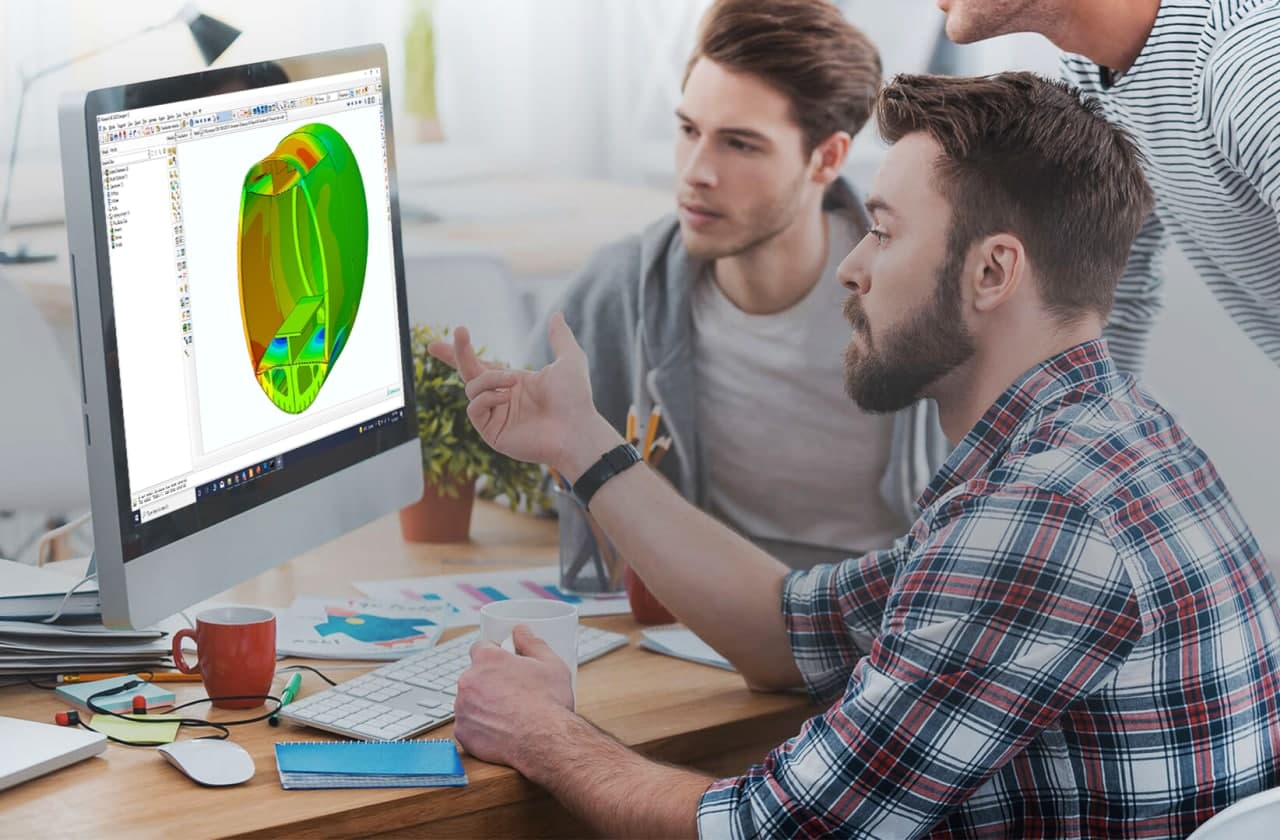
Telegram: +98-915-55-20-388
WhatsApp: +98-915-55-20-388
Find Us on WeChat

Reviews
There are no reviews yet.