Coupled Thermal Stress Analysis of Automotive Disc Brake
A coupled thermal-stress analysis considers the interaction between temperature, stresses, and deformation in the disc brake. This provides a more accurate prediction of brake behavior compared to separate thermal and stress analyses. The high temperatures generated during braking induce thermal stresses and strains in the brake components. A coupled analysis can accurately determine these thermal stresses.
The thermal stresses cause warpage and distortion of the brake disc and caliper, affecting brake performance. A coupled analysis can predict the extent of distortion under different braking conditions. Thermal stresses subject the disc brake materials to cyclic loading, reducing fatigue life. A coupled analysis provides a better estimate of brake durability.
The high temperatures accelerate material degradation in the brake pads and discs. A coupled stress analysis considering temperature-dependent material properties can model this effect. Residual stresses remain in the disc brake after cooling due to non-uniform thermal strains. A coupled analysis can predict these residual stresses.
Experimental validation of the disc brake model requires coupled thermal and stress measurements. A coupled analysis enables direct comparison with validation test data.
a coupled thermal stress analysis captures the interaction between temperature, stresses, and deformation in disc brakes more accurately. It provides valuable insight into factors like stresses, distortion, fatigue life, wear, and material degradation which influence brake performance and durability. The results from a coupled thermal stress analysis can then be used to optimize disc brake design for improved heat dissipation, lower stresses, and longer service life.
Verification & Validation (V&V)
In this Abaqus tutorial validation, a 3D dimensional coupled thermal stress analysis of the CA7220 automobile disc brake has been done using the Abaqus finite element analysis (FEA) software. The results of this FEA simulation have been validated with a known paper (Gao & Lin, 2002). For this analysis, the pressure from the pad to the brake disc is modeled and the heat generated by the friction between the pad and the disc brake is investigated. The final temperature distribution of the disc and brake pad is used to optimize the brake system.
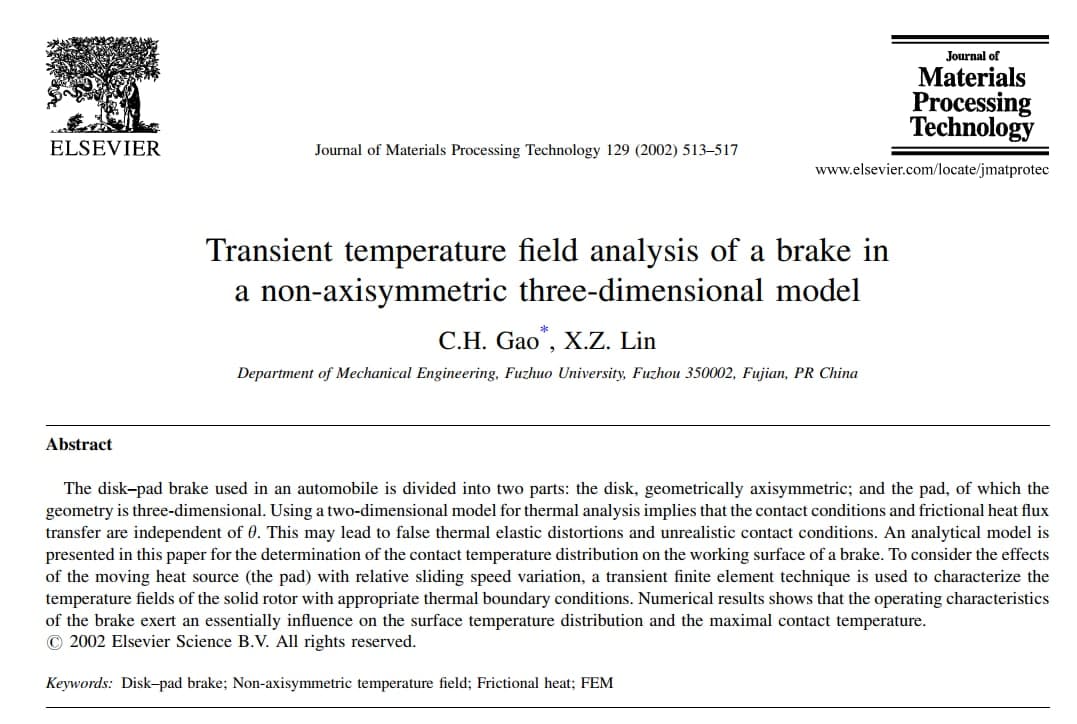
Gao & Lin, (2002) paper used for validation in this project
What you’ll learn
- How to model automotive solid disk brake and pad
- What material properties are used in transient thermal analysis
- How to use coupled temp-displacement step in Abaqus
- How to model the interaction between automotive solid disk brake and pad
- What interaction properties are needed for transient coupled thermal analysis
- What constraint must be used in this type of FEA simulation
- How to rotate a deformable part in Abaqus
- How to import and use graphs from paper as Amplitude in Abaqus
- What load and boundary conditions should be used?
- How to define the initial temperature for parts
- Practical points for mesh generation
- What is a mesh sensitivity study in FEA and how to do it in Abaqus?
Need help? Get a consultation from our experts.
Telegram: +98-915-55-20-388
WhatsApp: +98-915-55-20-388
Disc brake failures
Disc brake failures due to thermal issues are some of the most common. Here are a few examples:
- Warped discs – As the discs get overheated during repeated heavy braking, the material can expand unevenly and warp the disc surface out of shape. This causes vibrations and uneven braking performance.
- Glazed discs – The disc material can actually melt from extreme heat and re-harden in a glossy, smooth film on the surface. This severely reduces friction and braking performance.
- Cracked discs – Thermal shock from excessive heat can cause the discs to develop cracks, either radially across the disc surface or circumferential around the disc. Cracked discs need to be replaced.
- Frosted discs – When discs cool down very quickly after being overheated, water vapor in the air can condense on the hot disc surface, leaving a white ‘frost’ layer. This reduces the friction coefficient and braking power.
- Damaged piston seals and boots – The extreme temperatures in the caliper assembly can cause the piston seals and boots to degrade prematurely, leading to fluid leaks and loss of pressure.
- Reduced pad life – Pads wear out much faster when they are exposed to excessive heat. The friction material breaks down and loses its effectiveness.
The main factors that contribute to thermal issues are:
- Repeated hard braking from high speeds or down long grades
- Extreme ambient temperatures (both hot and cold)
- Inadequate ventilation of the discs
- Improper pad selection for the application
Course Content
- Introduction
- Purpose of validation
- Factors considered in disc brake analysis
- Overview of the validation approach
- Abaqus FEA Model Development
- Disc and pad geometry creation
- Material properties
- Assemble the parts
- Interactions
- Meshing
- Boundary conditions and loads
- Analysis steps
- Temperature Validation
- Experimental temperature measurement techniques
- Infrared thermography
- Embedded thermocouples
- Comparing Abaqus and experimental temperatures
- Sources of error
- Conclusions and Recommendations
- Summary of validation results
- Limitations of the model
- Suggestions for future improvements
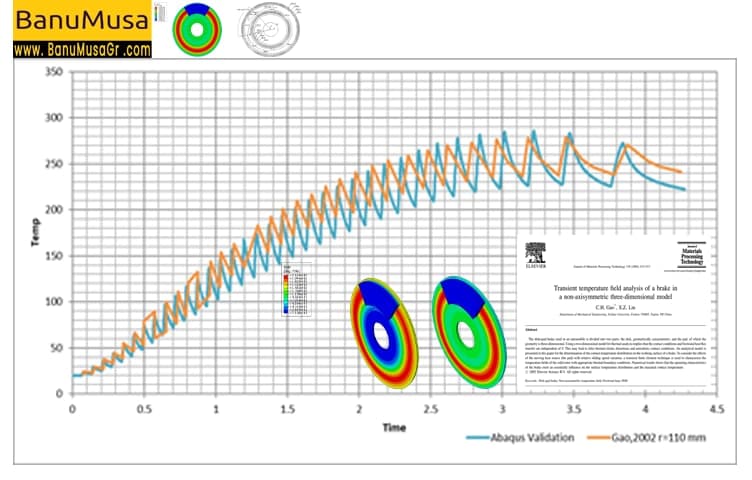
Who this course is for
- Automotive and mechanical engineers who need to perform thermal stress analysis
- Advanced students, Ph.D. students, or researchers for their Abaqus FEA projects
- Any Abaqus Application Engineer who is involved with various simulation projects on a daily basis
- Design and research and development (R&D) offices of automotive and parts manufacturing companies
- FEA simulation consultancies
What you’ll gain
- You will be able to conduct thermal stress analysis by Abaqus
- You can use the FEA results of this simulation for low-cycle fatigue analysis
Reviews
There are no reviews yet.