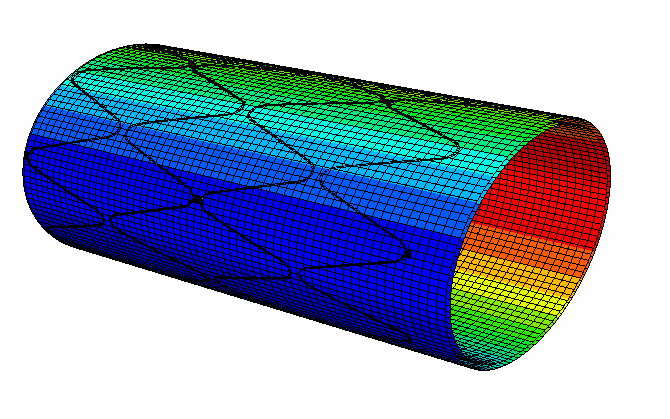
Composite Impact Simulation
Composite impact simulation: High-velocity impact on composite structures is a phenomenon that engineers in various industries such as aerospace, marine, and automotive should focus more on.
In this project, the impact on the laminate composite structure was studied. In these FE simulations, Abaqus finite element analysis software is used.
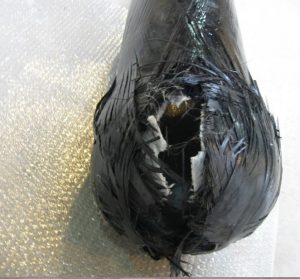
Composite impact simulation – Composite overwrapped pressure vessel
In order to simulate the damage in the composite, the model of the FRP composite material was used along with the degradation criterion and its evolution law.
This model has the ability to grow damage gradually. Many problems related to numerical simulations such as instability and dependence of the results on the size of the element tried in this model are reduced as much as possible.
High-velocity impact simulation of composite structures needs to account for strain rate effects, progressive damage, appropriate failure models, non-linear geometry, transient dynamic effects, contact constraints, rigid impactors and validation data to accurately predict damage initiation, failure loads and energy absorption characteristics.
Composite Impact Resistance
Comparing several different composite plates, it was concluded that the composite plates show good impact resistance. In these simulations, in order to better analyze different modes of damage, it can be observed.
These modes include matrix cracking, fiber breakage, and cracking. To simulate delamination, the Cohesive Zone Model was used due to its advantages over other methods such as VCCT.
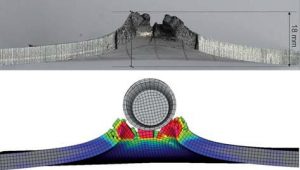
Composite impact resistance
Impact Analysis of Composite Pressure Vessels
Impact analysis is important for composite pressure vessels for the following reasons:
- To ensure safety – Composites have different failure mechanisms compared to metals. Impact damage can cause hidden damage that may lead to unexpected failure at lower loads. The impact analysis helps detect such damage to ensure the safety of the pressure vessel.
- To detect impact damage – Impact damage may not be externally visible in composites but can significantly reduce the strength and load-carrying capacity. Impact analysis using NDT (non-destructive testing) techniques can detect such internal damage.
- To assess residual strength – After an impact event, it is important to assess the residual strength and performance of the composite pressure vessel. The impact analysis helps determine if the vessel is still safe to use at the design loads or needs to be repaired/replaced.
- To determine repair needs – If impact analysis reveals significant damage, it can help determine the extent of repair or replacement needed for the pressure vessel to function safely again.
- To improve design – By understanding the impact behavior and damage mechanisms of composite pressure vessels, manufacturers can improve the design to make them more impact resistant in the future.
So in summary, impact analysis helps ensure the structural integrity, performance and safety of composite pressure vessels throughout their lifespan and also provides insights to improve future designs.
Composite Impact Simulation Results
- Design-by-analysis of composite pressure vessel
- Filament wound composite pressure vessel simulation & analysis with WCM plugin in Abaqus
- Low-velocity impact analysis for composite pressure vessels
- High-velocity impact analysis for composite pressure vessels
- Residual burst-pressure analysis of composite pressure vessels
- Buckling & post-buckling analysis of composite pressure vessel
- Cyclic & fatigue analysis of composite pressure vessel – Read Helius PFA course
Codes & Standards for Impact Analysis
There are a few key standards that specify requirements and test methods for low-velocity impact analysis of composite pressure vessels:
- ASTM D7136 – Standard Test Method for Measuring the Damage Resistance of a Fiber-Reinforced Polymer Matrix Composite to a Drop-Weight Impact Event. This standard specifies the test method for impacting composites and measuring the impact energy required to initiate damage. It can be used to evaluate impact resistance.
- ISO 18809 – Reinforced plastics composites – Determination of the effects of low-velocity impact. This ISO standard specifies a test method for impacting composites using a falling weight impactor and measuring parameters like impact force, energy and deformation.
- ISO/TS 15656 – Reinforced plastics piping systems for flame-resistant transport of fluids. This ISO technical specification includes requirements for impact testing of piping systems made of reinforced plastics, including impact energy and deformation limits.
- ASME PCC-2 – Pressure Vessels for Human Occupancy. This ASME standard includes guidelines for impact testing composite pressure vessels that are intended for human occupancies, like spacecraft and submersibles. It specifies impact energy levels for testing.
- Military standards – Various military standards also specify impact testing requirements for composite pressure vessels and containers used for military applications.