Low Velocity Impact on FRP composite plate in LS-Dyna
3D modeling techniques for low-velocity impact FRP laminate with LS-DYNA
The LS-DYNA Tutorial: 3D Modeling Techniques for Low-Velocity Impact Analysis of FRP Composite Laminate course offers a detailed exploration of the fundamental concepts and practical methodologies involved in simulating low-velocity impact on FRP composite laminates. Participants will learn the step-by-step process of creating accurate 3D models using LS-DYNA, a powerful finite element analysis software. The course covers topics such as material modeling, meshing techniques, boundary conditions, and impact loading scenarios specific to low-velocity impacts.
Participants will gain insights into interpreting and analyzing the simulation results to evaluate the laminate’s response to impact, including damage initiation, propagation, and energy absorption characteristics. Practical examples and case studies will be utilized to reinforce the concepts and enhance the learning experience. By the end of this tutorial, participants will have the necessary skills to perform reliable and effective low-velocity impact analysis of FRP composite laminates using LS-DYNA.
Progressive damage model
In order to effectively describe the progressively intralaminar and interlaminar (delamination) damage for FRP composite laminates, a three-dimensional progressive damage model for composite laminates is defined. It is used for low-velocity impact analysis of FRP composite laminates in LS-Dyna FEA software.
Progressive damage in FRP (Fiber-Reinforced Polymer) composites refers to the gradual development and propagation of damage within the material under various loading conditions. FRP composites are composed of reinforcing fibers, such as carbon or glass, embedded in a polymer matrix, typically epoxy resin. Progressive damage occurs when these materials undergo mechanical loading, leading to the initiation and growth of various forms of damage, including matrix cracking, fiber breakage, delamination, and fiber-matrix debonding.
The progressive nature of damage means that it starts as localized micro-scale damage, which then extends and interacts with neighboring regions, eventually affecting the overall structural integrity of the composite. This damage progression can occur due to factors such as cyclic loading, impact events, or long-term exposure to environmental conditions.
Understanding and predicting progressive damage in FRP composites is crucial for ensuring the structural reliability and safety of composite components. Advanced modeling and analysis techniques, such as finite element analysis (FEA) and cohesive zone modeling, are employed to simulate and predict the initiation, propagation, and interaction of damage mechanisms in FRP composites. By studying progressive damage, engineers can optimize composite designs, develop mitigation strategies, and assess the remaining strength and life of FRP composite structures.
Chang-Chang failure criteria
The three-dimensional progressive damage model is based on continuum damage mechanics (CDM) and is implemented in the LS-Dyna with Chang-Chang failure criteria (*MAT_054). The nonlinear damage model can be used to analyze the dynamic performance of the composite structure and its failure behavior.
For the interlaminar damage, 3D cohesive elements with *MAT_138 material keyword are used. The FEA model is validated by a well-known paper (Guo et al. 2013) and can be used in any simulation.
What you’ll learn
In this LSDyna tutorial video, you will learn how to use the *MAT_054 composite material keyword & *MAT_138 cohesive material keyword in LS-Dyna and determine their parameters. How to model the damage in the FRP composite laminates, its damage modes, selecting the appropriate element in accordance with the analysis, orientation of composite modeling, contacts, and many other techniques.
Overview
- Geometry and Meshing
Techniques for creating accurate 3D models of FRP composite laminates, including proper meshing strategies for impact analysis. - Material Modeling
Understanding the material properties and behavior of FRP composite laminates under low-velocity impact conditions.- *MAT_COHESIVE_MIXED_MODE material keyword(*MAT_138)
- Define cohesive damage parameters
- Mechanical and damage properties of Composites
- Composite damage modes
- Cohesive damage modes
- Defining Fibre Orientation (Material Direction) using LS-PrePost
- Element selection
- Rigid Elements
- FRP composite laminate elements
- Boundary conditions (BC)
Setting up appropriate boundary conditions to simulate realistic loading and constraints during low-velocity impact. - Impact Loading
Different types of impact loading scenarios and their effects on FRP composite laminates. - Damage Modeling
Techniques for modeling and predicting damage initiation, propagation, and energy absorption in the laminate. - Visualization Techniques
Image, Movie, Plots, &, etc. - Analysis and Interpretation of Results
Evaluating and interpreting the simulation results to gain insights into the laminate’s response to low-velocity impact. - Case Studies and Practical Examples
Real-world examples and case studies demonstrating the application of LS-DYNA for low-velocity impact analysis of FRP composite laminates.- Simulation of low-velocity impact on FRP composite laminate
- FEA validation By Guo et al. paper (Contact force, delamination & cracking damage modes)
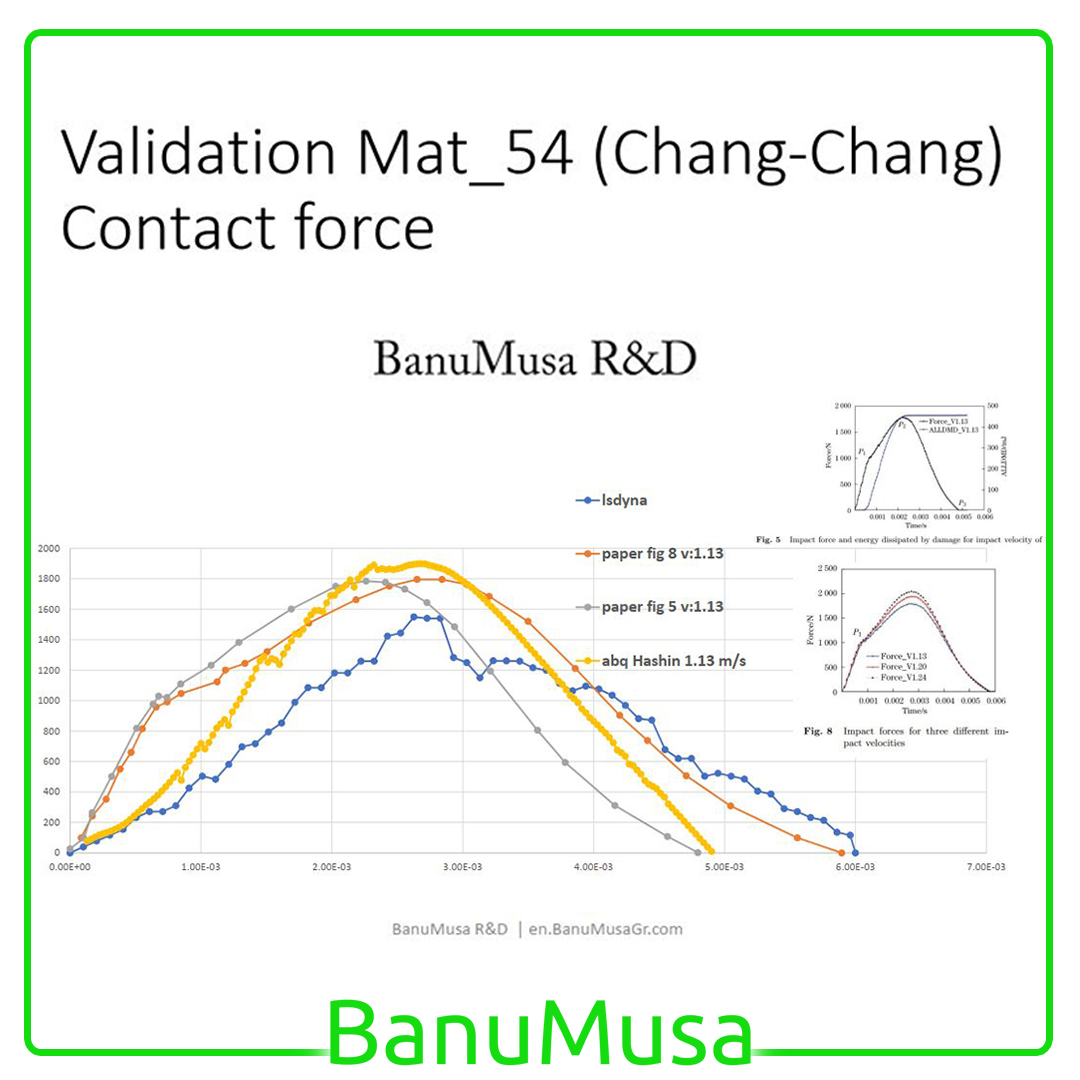
Need help? Get a consultation from our experts.
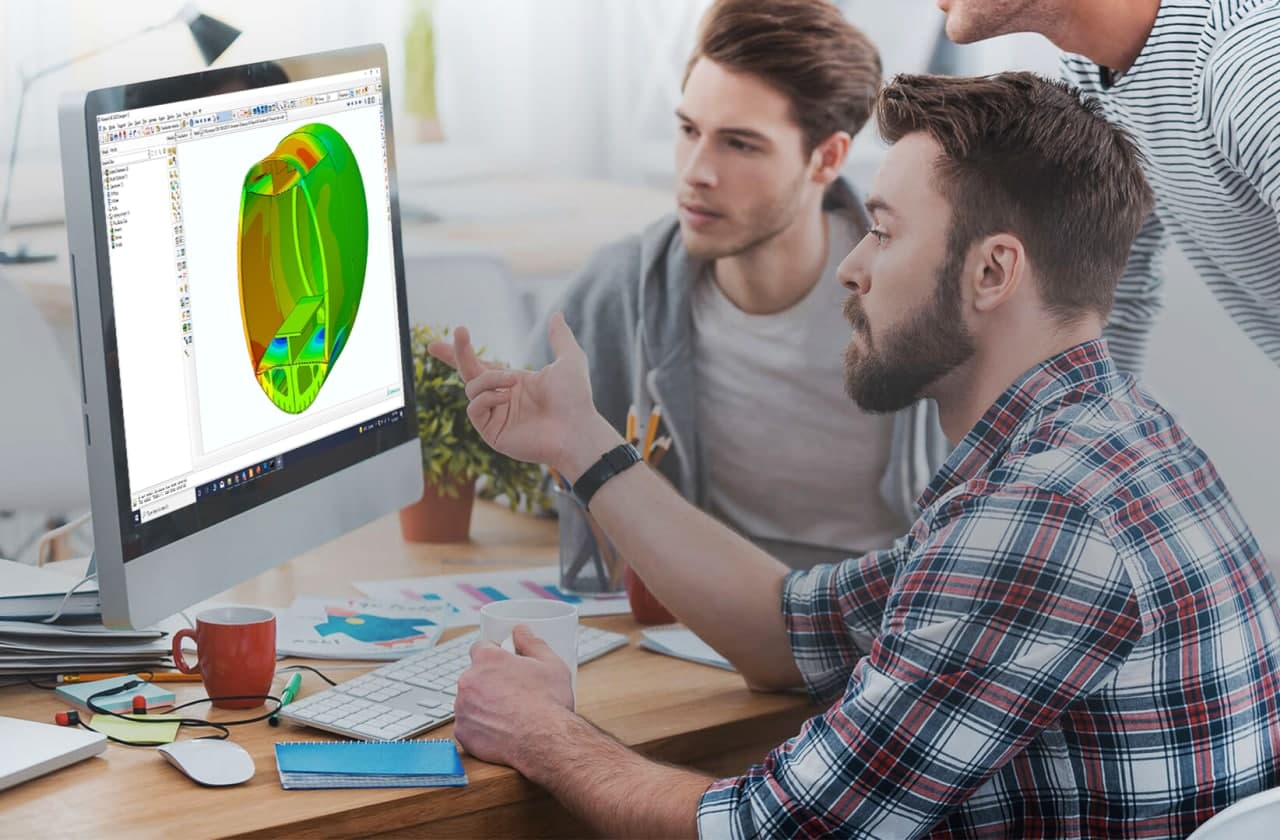
Telegram: +98-915-55-20-388
WhatsApp: +98-915-55-20-388
Find Us on WeChat
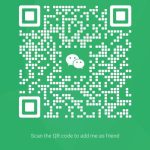
Who this course is for
- Civil and mechanical engineers who need to perform low-velocity impact analysis
- Advanced students, Ph.D. students, or researchers for their LS-Dyna FEA projects
- Any LS-Dyna Application Engineer who is involved with various simulation projects on a daily basis
- Design, research, and development (R&D) offices of military and parts manufacturing companies
- LS-Dyna FEA simulation consultancies
What you’ll gain
- You will be able to conduct low-velocity impact analysis by LS-Dyna
- You will be able to develop your own LS-Dyna FRP composite laminate damage model
Reviews
There are no reviews yet.